We choose pipes for electrical wiring, taking into account the characteristics of the product and the building
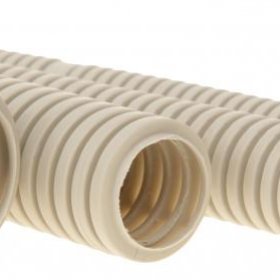
The main cause of fires due to a short circuit is the use of outdated technology for wiring without protective pipes. If you plan to repair a room or a house, we recommend that you familiarize yourself with modern requirements and ways to ensure safety.
Content
Scope of use of pipes for electrical wiring
Even 10-15 years ago, conductive wires were hidden in pipes only in cases where they needed to be protected from mechanical, chemical or thermal effects. Pipes were used to create a common entrance to the building, when laying cables in the ground at a shallow depth, and electrifying buildings with high fire safety requirements.
According to modern building standards, all conductive cables, regardless of the thickness of the insulation and the cross section of the core, must be hidden in pipes that are suitable in diameter. This rule not only ensures the safety of wiring, but also helps to avoid a fire during a short circuit. Pipes are used in warehouses, industrial buildings, residential individual and multi-apartment buildings. An exception may be only rooms with open wiring and low fire safety requirements.
The main functions of pipes for electrical wiring:
- Cable Shock Protection. The integrity of the wire hidden in the plaster may be compromised when mounting the shelves or creating a new opening in the wall. If the wire is in the pipe, the probability of this damage will be significantly lower.
- Moisture proof wiring. For example, if the apartment is flooded with neighbors from above, the wires laid in the ceiling will fall into a humid environment and if they are not protected, then a short circuit may occur in the connection points and in areas with impaired insulation.
- Fire prevention. The tube will not allow the fire to affect neighboring areas or significantly limit its intensity (depending on the material of the product). In wooden houses, this is an effective way to stave off a fire and enable owners to prevent a fire.
- Ease of repair. If the wire leading to the outlet is damaged, no walls will be required to restore its operation. The wizard simply disconnects its end in the junction box and, attaching the edge of the new cable to the free end, pulls them to the outlet through the pipe. As a result, the old cable is completely pulled out, and the new one will only be connected to the contacts. All the work will take no more than 30-40 minutes and will cost ten times cheaper than reworking the entire wall.
Types of pipes
Pipes are divided depending on the material into metal (from steel, copper, aluminum) and plastic (from PVC, HDPE). Each of these materials can be used for the manufacture of both smooth straight and corrugated pipes.
Smooth steel
Steel pipes are a traditional but the most time-consuming way to protect the wiring from any mechanical influence, pollution, ultraviolet radiation. They are most often used when supplying electricity to a building, at the intersection of floors and laying wiring in the floor. In agriculture and industry, wiring in steel pipes is equipped in warehouses with fuel, grease, varnishes, acetone-containing substances and other explosive or fire hazardous materials (according to GOST 3262–75).
Since such pipes are still considered the most reliable, GOST 10704–91 and GOST 10705–80 recommend installing them:
- in all types of child care facilities;
- attics of buildings of any purpose;
- in buildings of a cultural and entertainment nature;
- hospitals and sanatoriums;
- in hot industrial plants;
- behind suspended ceilings and in complex foundations for equipment.
In explosive rooms, the line is laid in thick-walled pipes with internal galvanization and a threaded coupling. If there is only a danger of fire (without explosion), it is allowed to use thin-walled steel pipes that are connected by sleeves and cuffs. But when it is necessary to protect the wires also from dust, harmful fumes or high humidity, you should choose pipes with a male-threaded connection and a sealant.
Since steel pipes are prone to corrosion, it is necessary to select products with a protective coating or paint them with Kuzbasspack after installation. Such painting must be renewed every few years if the pipe remains in the open. The product is also suitable for laying in the thickness of the wall under the plaster and in the floor in the screed.
Mounting Features
Clutchless pipes can only be installed by an experienced welder with an appropriate tolerance level. The bends of the pipeline are carried out due to the connection of complete corner elements (welding or thread). The length of the section with two bends should not exceed 5 m, after which it is required to install a junction box.
The order of installation of steel pipes for wiring:
- pipe cutting, according to the sketch;
- a complete set of blanks in knots and blocks;
- cleaning the inner surface of the pipes (if there is no galvanization there);
- painting or varnishing of pipes, if they are laid outdoors;
- step-by-step assembly of the system and installation inside the wires.
Direct sections of the open steel pipe must be mounted with a slope towards the junction box so that condensed and rain water does not accumulate on the pipes.
Video: Creating wiring using smooth steel pipes
Advantages and disadvantages
pros | Minuses |
High mechanical resistance. | The complexity of installation. |
Suitable for hazardous areas. | The need to update the paint coat. |
Recommended for fire hazardous buildings. | Inability to use with cables without insulation. |
Protect wiring from dust and gases. | Bending angle limited to 90about, the length of the straight section is 10 meters. |
Increased resistance to both transverse and tensile loads. | Heavy weight, even for thin-walled products. |
The period of use is up to 50 years (depending on operating conditions). | High price. |
Corrugated steel pipe
Such products differ from smooth steel pipes in that they are not welded, but assembled from a strip using a movable joint. The resulting pipe has additional stiffening ribs, which further increases its resistance to lateral loads - up to 60 atmospheres and above. But because of the method of creation, it is more sensitive with tensile loads (with strong tension, the tape dissolves into a spiral).
Compared to smooth pipes, it is easier to install, since it does not require the use of corner elements. The tube itself bends in any desired direction, thin - even by 300about. Corrugated pipe does not connect, it remains solid throughout from the point of connection to the junction box, so the qualification of a fitter can be much lower than in the case of a smooth analog.
In addition, steel corrugation is usually made of high alloy steel, so it is not "afraid" of moisture, fungi, corrosion and does not require special care. As you can see, corrugated steel pipe is spared all the shortcomings of a smooth one, but its price is much higher than that of plastic counterparts.
Video: Assembling a corrugated pipe using a threaded connector
Copper pipes
Copper pipes are similar in weight to steel, mechanical resistance and many other characteristics. But they have much lower sensitivity to moisture and chemical agents, so copper and brass (copper-based alloy) products are used in rooms with a high content of water vapor: greenhouses, botanical gardens, car washes, bathhouses. This option is characterized by the longest service life, but its price is high.
Since copper pipes look very attractive, designers use them to create open decorative wiring. Such a system looks especially impressive in combination with retro-switches and copper, brass or bronze chandeliers (or their imitation). Due to the high weather resistance of copper, such wiring can also be used to decorate the facade of the building. The greenish-blue coating, which gradually appears on the surface of the metal due to oxidation, does not spoil the appearance of the product, but only makes it more decorative.
Mounting Features
Copper pipes are not always connected by couplings; thin pipes simply bend at the right angle. Despite the increased (compared with steel) ductility of copper, only an experienced welder with equipment suitable for working with thin-walled products can mount such a pipeline. The restrictions on the length of the straight section, the bending radius and the location of the junction boxes are the same as for steel.
Plastic pipes
Smooth-walled and corrugated pipes from different types of plastic (PVC, HDPE, LDPE) are used for laying electric cables. They differ in mechanical and thermal properties, but have a number of common features:
- Low weight, which facilitates the installation process, transportation and storage. With a large number of pipes in buildings with weak wooden floors, plastic ones should be preferred precisely because they load the building construct less than metal.
- Easy installation. Even a beginner can cope with styling, since the welding process is not required and the use of connecting elements is not necessary. To fasten the pipe to the base, just snap it into a special plastic clip.
- Suitable for mounting cables without their own insulation. Metal pipes for this purpose are prohibited.
- Low linear expansion coefficient. This means that when heated, the pipe practically does not increase its diameter, therefore, when laying the cable in the thickness of the wall, cracks do not appear in it.
- Low cost in comparison with metal counterparts.
Plastic pipes may be used for underwater cabling.
Manufacturers produce hard, soft, reinforced and corrugated products for use in various conditions. For example, rigid ones are recommended for laying wiring under plaster.
The differences between plastic pipes for wiring
Type of pipe | PVC | PND | LDPE |
Material | Polyvinyl chloride | Low-pressure polyethylene | High pressure polyethylene |
Fire resistance | Up to 650about C, does not support combustion | Up to 130about C, supports combustion | Up to 110 about C, supports combustion. |
Permissible temperature amplitude in the room | -25about — +60about FROM | -50about — +40about FROM | -60about — +40about C (in case of an accident +80about FROM) |
UV Resistance | Low, the product is not used for open wiring. | Low, depending on the chemical composition (some manufacturers add special additives). | Low |
Chemical resistance | Medium, approved for use in gassed rooms. | Good, not afraid of gases. | Low, easily oxidized by chemicals, including gaseous. |
Water permeability | Almost absent, suitable for underwater communications. | Low, suitable for rooms with high humidity. | Low, laying underground is possible in places where significant mechanical loads are not expected. |
Term of use | Up to 50 years | 40-50 years (depending on operating conditions). | More than 50 years. |
Video comparison of different types of plastic pipes
Plastic pipes are suitable for laying conductive cables, telephone, alarm and telecommunications in residential buildings, as well as in industrial and administrative buildings.
HDPE pipes are 6 times lighter than steel.
Smooth plastic pipes
PVC products are available in lengths of 3 m with a range of diameters from 16 mm to 50 mm, according to TU-6–19–215–83 (their specifications are not regulated by GOSTs). Products are allowed to be used not only for laying hidden wiring in non-combustible materials, but also in low-combustible ones. That is, in them you can lay the attic wiring between the layers of stone wool.
PVC pipes do not need to be protected from corrosion, fungus, weak chemical oxidizing agents.
Not all PVC pipes are self-extinguishing. When buying, be sure to check the sample in the store.
Corrugated plastic pipe
Plastic corrugated tubes are offered in bays 25, 50, 100 and 200 meters long. This makes it possible to create wiring without unnecessary connections, which increases the reliability of the system. But if the circuit is very complex, it is permissible to use couplings, bends, tees and sleeves.
Given the relatively low resistance of plastic to mechanical shock loads, corrugated pipes are recommended for laying in the thickness of the wall or in hard-to-reach places (for example, behind a stretch ceiling canvas).
Selection of the diameter of the PVC pipe, depending on the purpose
Destination |
Corrugated Pipe Diameter cm |
Power supply circuit breakers | 2,0 |
Power Outlets | 2,0 |
Lighting Power | 1,6 |
Phone and alarm connection | from 1,6 |
Connecting shields and junction boxes | 2,5 |
Providing interfloor connections | 4,0–5,0 |
Features of the installation of plastic pipes
When laying the cable in a plastic pipe, it must be placed at least 10 cm below the heating pipe to prevent heating of the conductive wire. If these elements are not laid in parallel, but intersect at one point, the height difference should be between 5 cm.
Light corrugation cannot be poured with concrete, it is deformed by pressure. Look for tight.
In wet rooms, the connection points of the pipe to the junction box must be sealed.
It is unacceptable to hide the wire connection inside the plastic pipe. If the cable is shorter than necessary, a junction box is placed at the junction.
For grounding and grounding of wires, special jumpers and nuts are used.
When cutting a plastic corrugation, be careful not to scratch your hands with a wire stretched inside.
Installation of smooth plastic pipes: video tutorial
We choose pipes for installation in different conditions
Please note:
- Pipe diameter. The wider the bell, the thicker the wire can be laid in the pipe.
- Material Density / Wall Thickness. Thin-walled pipes are used only in areas with low mechanical stress.
- Length of segments (required and production). If the scheme has a large number of straight sections longer than 3 meters, it will be more economical to use a corrugation.
- Possibility of bending. A large number of turns will require the installer to solder / weld many connecting elements. Using corrugations will be easier to work and cheaper.
- Product weight. If in an old house it is important not to overload the floors, it is better to prefer plastic.
Selection of a metal pipe depending on the material and cross-section of the wire
Wire material |
Wire cross section mm2 |
Pipe thickness for wiring, mm |
Copper | 4,0 | 2,8 |
Copper | 6,0–10,0 | from 3.2 |
Copper | 16,0 | 3,5 |
Copper | 25,0–35,0 | 4 |
Aluminum | 6,0 | 2,5 |
Aluminum | 10,0 | 2,8 |
Aluminum | 16,0–25,0 | from 3.2 |
Aluminum | 35,0–50,0 | 3,5 |
An important role in choosing pipes is played by the operating conditions of the system:
- Underground communications. In such conditions, the mechanical resistance of the product, water resistance and the ability to seal are put in the first place. Building regulations allow the use of double-walled plastic corrugated pipes with a diameter of up to 20 cm for underground cable laying. Thicker cables are laid in metal products. The steel pipe for such wiring should have a wall thickness of 2 mm or more. If there is a possibility of damage to the cable with a sharp object (for example, the cable passes in the country under a flowerbed), you should choose a steel pipe with a protective coating and internal galvanization, and use sealing gaskets when connecting.
- Wet rooms. In such cases, it is required to ensure complete sealing of the cable and at the same time select pipes that are resistant to moisture. For this situation, smooth plastic pipes are recommended, which are fused with connecting elements as a whole (as in a water supply system).
- Buildings with increased fire safety. Here the main role is played by the resistance of the pipe to fire. For maximum safety, we recommend choosing thick-walled metal pipes with threaded connectors.
- Living spaces. Since there are a lot of electrical appliances in a residential building, ease of installation and compact wiring are very important here. Best of all, PVC corrugation meets these requirements. This option has sufficient resistance to fire and mechanical stress for living quarters.
If, after reading the article, something remains unclear, we recommend that you entrust the work to an experienced installer and buy materials with him. To those. who is going to do the installation on their own, we recommend that you take careful measurements of the room at home and perform the necessary calculations together with a consultant in the electrical goods store.
1 comment