Homemade hand drill for drilling: spiral and spoon designs
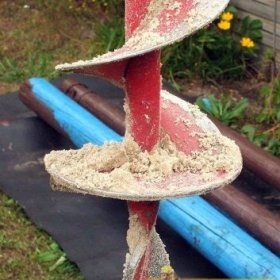
Drilling shallow wells in soft soils can be done using a makeshift device. The maximum possible depth of the borehole in this case can be 20 meters. One of the components of the design is a split drill pipe, the length of which increases with the depth of the well. Another important element is the handle, which allows you to rotate the pipe to one person or two together with an assistant manually with the application of physical effort. The main element of the hand tool, of course, is the drill, which can be done in several ways. But if you decide to make a drill for the well with your own hands, then you must make it out of metal, so the master must have welding equipment and the skills to work with it.
This video shows how to make a drill for a well in a couple of hours. Judging by the reviews, the advice of the author of the video helped many beginner self-made masters in practice.
Self-made spiral drill
In the simplest embodiment, the spiral drill is made in the form of a metal rod with a well-pointed end. A pair of knives is welded 200 mm from the tip tip. For the manufacture of knives, halves of a steel disk are taken, 100-150 mm thick. The knives are welded to the metal rod at a small angle, the value of which is no more than 20 degrees to the horizontal. In this case, the halves of the steel disk should be located opposite each other. As a result, the angle between the welded knives is 40 degrees.
The lower edges of the cutting elements of the hand drill for well drilling are also well sharpened. The speed and ease of cutting the tool into the ground depends on how sharp the knives are.
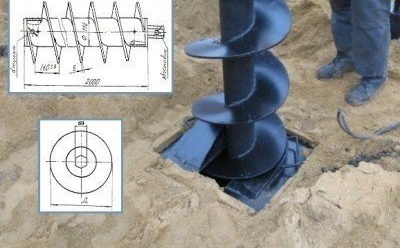
The factory-made spiral drill is made from special tool steel, which is heated, and then twisted into a spiral and hardened
Industrial models of drills of this type are manufactured in the factory from a strip of tool steel, heated and twisted into a spiral. The pitch of the turns of the spiral is equal to their diameter. After twisting, the steel is hardened.
How to work with a spiral drill?
Homemade tool during the rotational movement produced by the worker with the help of a handle, crashes due to pointed knives into the soil layer. Then a manual drill for wells is pulled out along with the cut soil up. Earth pours out to the side of the drilling site. The operation is repeated again.
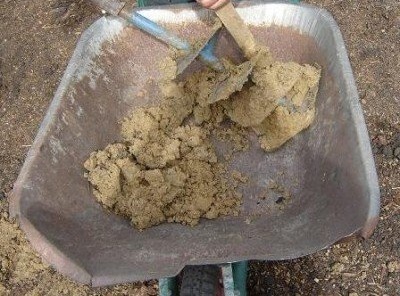
Purification of a home-made spiral drill from the soil raised from the wellbore up is carried out near the place of work and transported from the site on a trolley
With an increase in the depth of the structure, the tool rod is extended. In this case, the constituent elements are fixed to each other using a threaded or sleeve type of connection.To secure against separation of the components of the rod, their connections are additionally fixed with cotter pins.
Raising the elongated tool up, remove the additional links of the rod. The spiral drill copes well with clay soils, as well as with fine gravel that falls in the way of its moving deeper into the mine.
Features of the device of the spoon type drill
In soil resistant to shedding (loam, wet sand, etc.) it is more convenient to use borax spoons. Homemade spoon drill for wells is made in the form of a cylinder, in the side surface of which a longitudinal slot is made. Sometimes the shape of this slot takes a spiral shape. The length of the borax spoon is usually not more than 700 mm. The recovered rock is held in the cylinder cavity due to its compression and adhesion. Than loose soil, the already there should be a cut in the tool. To obtain a cylinder, you can take sheet steel and roll it to a given diameter. The easiest way is to choose a suitable piece of pipe, originally having a cylindrical shape.
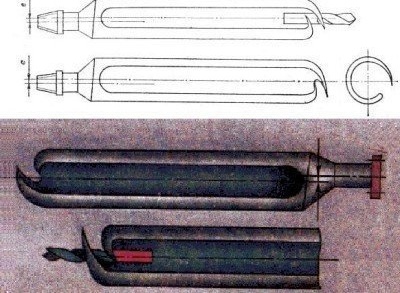
A home-made manual drill spoon is made of a piece of pipe of suitable section, in the lateral surface of which a longitudinal or spiral-shaped slot is made for excavation from the side walls of the well
A bur spoon makes excavation not only with its horizontally located lower edges, but also with a vertical edge. In this case, the soil accumulates in the cavity of the cylinder. In some cases, a conventional metal drill is welded to the bottom of the structure, which must be positioned strictly along the axis of the rod.
The main feature of the drill bit lies in the fact that the axis of the drill and the rod coincide, while the line of the axis of the body of the manual drill along with the cutting longitudinal edge is shifted by a millimeter and a half relative to the center axis line. Due to this mutual arrangement of the axes, the tool manages to drill a borehole of a larger diameter than the drill itself. This is possible due to the removal of soil from the side walls of the shaft with a longitudinal cutting edge. To clean the tool from the removed soil, the drill is periodically raised upward.
It is important to note that the spoon drill passes quietly inside the casing, which is installed to prevent collapse of the well shaft.
Is it worth it to do manual drilling?
The advantages of a manual method of drilling include:
- low cost of work;
- the ability to operate a hand pump during power outages;
- preservation of the landscape of the site, because the arrival of special equipment is not provided.
The disadvantages include the existing restrictions on the possible depth of the structure. In addition, the operation of a homemade drill is almost impossible in dense soils.
Home-made drills for drilling wells can also be used in the construction of fences, planting plants, the construction of pile foundations and many other types of gardening and construction work. As you can see, to build such a good "assistant" is within the power of any artisan man who is used to using his own tools in the farm.