DIY bending machine
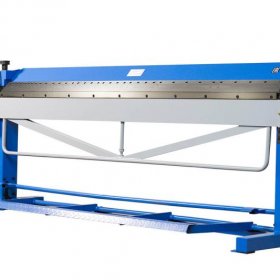
Modern sheet bending machines are popular designs for performing cold bending of basic sheet metals, if necessary, to facilitate the creation of various products. To make the simplest, but functional bending machine with your own hands is quite possible with little time, effort and money.
Content
What is a plate bending machine
Press brake or press brake - a device for cold bending of metal. The main purpose is the manufacture of products from sheet materials.
Due to the plasticity of the material, non-ferrous and ferrous metals, as well as many types of alloys, are easily subjected to mechanical stress. Bending machines allow you to bend metal products, giving them a round, square or shaped shape. In this case, the outer layer of the product is stretched, and the inner is compressed. A prerequisite for bending are accurate and even angles.
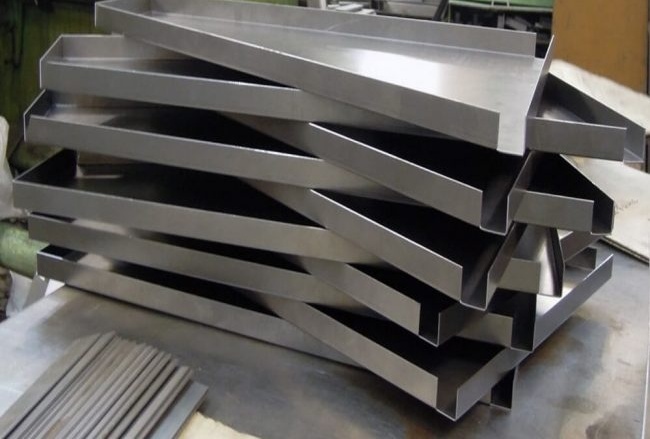
The main feature of metal bending is the absence of kinks, corrugation of the finished product and the appearance of other shortcomings
Often, sheet bending machines are used at the site of roofing, in construction, in the manufacture of all kinds of profiled sheets. Using bending machines create stand products and signs. The equipment is used in aircraft manufacturing, machine building, instrument making, in the petrochemical and shipbuilding industries. Thus, a modern machine is simply indispensable for bending a variety of products based on sheet metal.
History of Technical Development
As early as in the first half of the last century, the world industry produced mainly bending machines of a mechanical type, which was explained by the low cost and ease of execution, as well as the reliability of operation of such devices. Nevertheless, mechanical presses had significant shortcomings, associated primarily with their massiveness and the growth of basic requirements for enterprises.
Mechanical structures consumed a significant amount of electrical energy, were noisy and very vibrating.
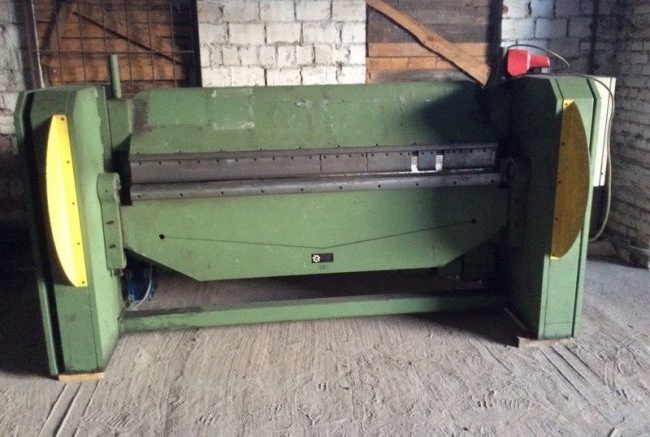
The very first devices are characterized by the complexity of frequent changeovers and too high a risk of injury, as well as the low quality of finished products
Pneumatic-type bending constructions are limited in operation due to the need to provide a supply line with compressed air.And mechanical models are not practical in industrial applications because of the rather low quality characteristics of finished products and low productivity. Therefore, the development of modern technology easily made it possible to develop hydraulic bending machines. Work on such machines contributed to the manufacture of products with high quality, and the press itself was distinguished by high reliability and low level of electrical energy consumption.
The appearance of new control systems in the design complemented the devices with a convenient graphical user interface with automatic calculations of the entire sequence of operations and program steps, and protection with a complex laser monitoring device. The most modern units are fully protected from overload pressure, have convenient electronic speed control, a control sensor and many other important improvements.
Types of bending machines
Bending machines can be stationary and mobile or mobile type, are divided into press, rotary and rotary models. Such a device is equipped with a hydraulic, pneumatic or electromechanical drive, and is also available in a mechanical and manual version with automatic or manual feed of the workpiece and with different types of CNC.
Simple hand
They function due to the use of muscular strength and a “rotary beam”, due to which the metal is given the desired shape with a lever. A significant part of hand-held devices is represented by mobile devices that are operated directly at the places of manufacture of metal products.
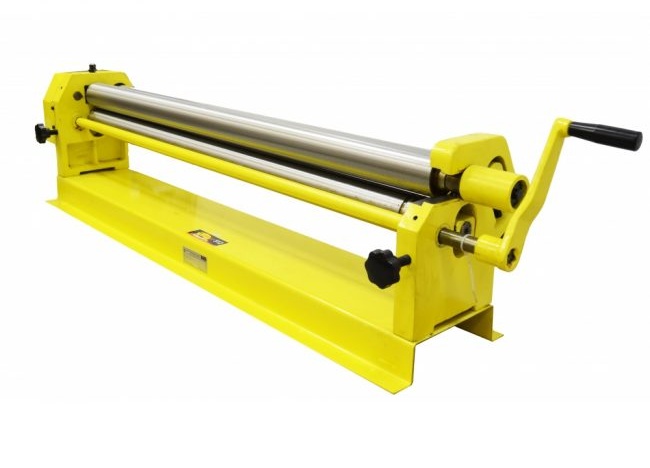
The frame of manual machines is made of stainless steel, which ensures the reliability of the entire structure
The advantages of a simple manual bending machine are represented by the absence of noise in operation, low cost, lightness and mobility, as well as independence from the mains. The disadvantages include the small width and the possibility of using exclusively thin tin in the work with a thickness of not more than 1.5–2.0 mm.
Pneumatic
The work is due to the presence in the design of pneumatic cylinders. Such press brakes are produced in the form of stationary and mobile models, but the most commonly used units are made according to the type of a traditional “swing beam”.
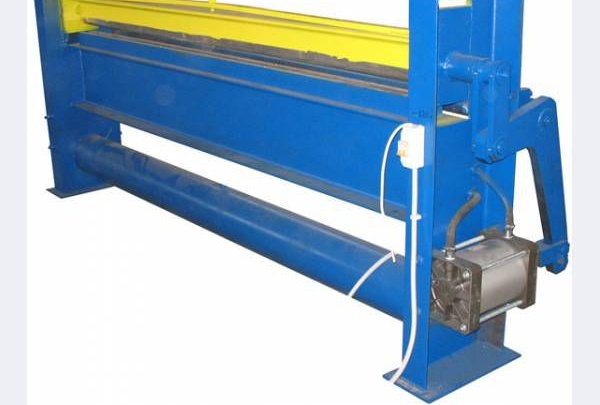
The machine allows the production of serial parts of various geometries, including those from sheet metal with paintwork
The advantages of a pneumatic bending machine are represented by good automation of the process, as well as high versatility and the need for minimal operator intervention in the entire process. In addition, pneumatics are quite affordable and easy to maintain. The most basic drawback of pneumatic type models is the need to provide a sufficiently powerful and expensive compressor that creates noise during operation.
Hydraulic
Mobile and stationary hydraulic sheet bending machines operate due to the presence of a hydraulic drive in the design. To date, this option is considered one of the best and most modern equipment.
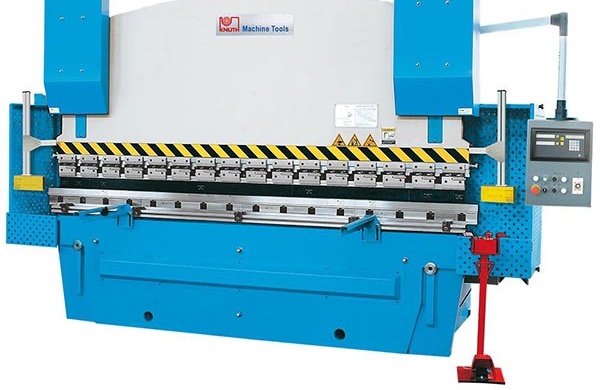
Modern hydraulic bending machines are used to obtain products that are ideal in quality and accuracy.
The advantages of the hydraulic type models are represented by fast operation, low noise, high reliability and the possibility of bending even thick metals. This kind of device rarely needs maintenance. The disadvantages of operation are the problems of searching for failed parts, the need for repairs in specialized workshops and the risk of oil leakage with significant wear.
Electromechanical
Stationary view of the bending machine, functioning due to the operation of an electric motor, drive system and gearbox.Electromechanical presses are deservedly very popular, due to the affordable cost and relative ease of use.
The advantages of electromechanical equipment are represented by a relatively low price, good performance, wide functionality and the availability of basic spare parts. When choosing, it is necessary to take into account such operating minuses as the significant noise of an electric motor, chain or belt, and not too high reliability indicators, which is explained by the presence of a large number of parts and basic components.
Mechanical
Stationary type mechanical bending machines function as a result of the transfer of kinetic energy from a previously untwisted flywheel to the desired performance.
Despite the low cost of production, simplicity of execution and rather high reliability of operation, mechanical machines are distinguished by their large mass, high level of consumption of electric energy, noise in operation and a noticeable inconvenience of independent readjustment.
DIY bending machine
The easiest way is to make a manual machine yourself, which is easy to use, but somewhat limited in functionality.
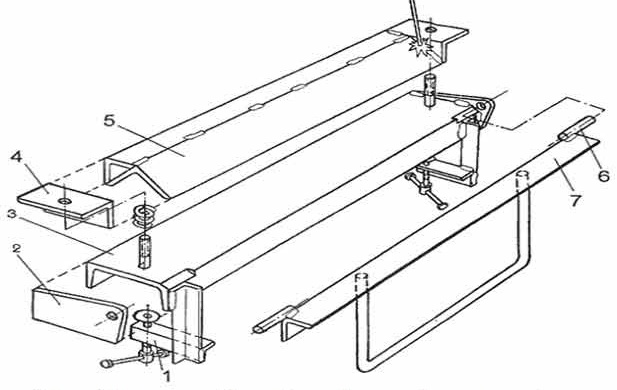
It is difficult to find a drawing of the device that would satisfy all requests, but you can refine the most successful template
- 1 - a clamp;
- 2 - cheek;
- 3 - base;
- 4 - bracket;
- 5 - clamp welded type;
- 6 - axis;
- 7 - corner of the punch.
It is necessary to minimize the number of machine elements that need to be ordered on the side, resorting to the help of revolvers or milling machines.
Work on this type of equipment requires high skill of the operator, which is explained by the increased risk of manufacturing defective products in the presence of even a slight skew of the installed workpiece. All manual models of self-manufacturing are simplified, but their main drawback is represented by the physical stress of the operator.
Preparation for work
An easy-to-make manual bending machine can be quite powerful, designed to work with metal sheets of different thicknesses. Before starting to manufacture such a model, you need to prepare all the necessary materials, as well as a welding machine, a drill with a set of metal drills and a grinder.
Basic materials for manufacturing:
- three standard angles having a shelf width of 45 mm or more with a metal thickness of 3 mm or more;
- brands on 70 mm - for bending the most thick and long sheet metal;
- two standard metal door hinges;
- a pair of screws with a diameter of 10–20 mm;
- "Lamb" for screws;
- spring;
- 0.5 cm thick metal for jibbing.
The workplace should be as flat as possible, strong and reliable, free from dust and any contaminants. In extreme cases, the manufacture of structures on the surface of the earth is allowed.
Step-by-step manufacturing process
There are several schematic diagrams and drawings of a homemade bending machine, but the most convenient to use and practical to use is a bending machine based on brands.
This DIY bending machine manufacturing option is easy to implement, but allows you to work only with fairly thin sheet metals.
- Two brands are folded neatly and evenly, after which notches are cut at two ends at a slanted angle of 45 ° for loops. The third brand must be cut in the same way.
- Metal door hinges are reliably welded without fail, not only from the front, but also from the wrong side.
- A pair of jibs are welded to each of the brands on two sides.
- A bolt nut is welded to the struts.
- A clamping bar is installed in the form of a third cropped brand, after which metal plates having a hole in the central part are neatly welded on the upper part. The diameter of this hole should slightly exceed the size of the bolt.
- The spring is installed in such a way that it can raise the pressure bar by about 0.5–0.7 cm. The bolt passes into the “ear” on the pressure bar, after which the spring is put on and the nut is tightened.
- A pair of reinforcing pieces, which are used as convenient and reliable handles for twisting, are welded to a screw cap. It is quite possible to install the spring on the screw, which will greatly facilitate the process of lifting the bar.
- The corners are not located on shelves in relation to each other, but have a one-sided direction, which makes fixing the loop not too convenient, but quite feasible.
- The clamping strip from the corner is laid upward on the machine, and the reinforcement made of ordinary metal jumpers prevents bending of the element. Not too small metal pads with holes drilled for bolts are welded at both ends of the plank.
- The clamping plate is installed on the machine, after which a spring is laid and handles are installed.
Ready listogib - a good home-made option for domestic use, which easily bends galvanizing and tin.
Safety precautions
Standard safety precautions provide for mandatory compliance with the manual for manual bending machines:
- setting the required bend angles on the stop;
- control of installed data by goniometer;
- checking the correct installation of the working tool;
- neat laying on the frame part of the device of the element for folding;
- performing test bending and, if necessary, making adjustments;
- repeated check of correctness of bending.
It is important to control the correct course of all bending operations, as well as to check the technical condition of the device in a timely manner, to maintain the listogib clean and tidy.
Advantages and disadvantages of homemade and purchased models
When choosing, you need to pay attention to technical capabilities and give preference to equipment that has a small margin for the main important characteristics. The most purchased machines are units manufactured by manufacturers from the USA, Poland, China and Germany.
Low-cost production machines include Chinese and Russian sheet bending machines, and mid-price presses include models from the USA, Turkey and Poland. The most expensive and inaccessible for ordinary consumers are considered machines from manufacturers in Germany and France, as well as manufactured by other West European countries.
Table: Comparison of sheet bending machines from different manufacturers
Brand | Mobility / Vandal Resistance | Device Repair Cost | Metal thickness / resource of the working part (p. M.) | Cost thousand dollars |
Tapco | High / low | High | 0,7 / 10000 | From 2.0 |
Van mark | High / low | High | 1,0 / 10000 | From 2.0 |
Jouanel | Low / high | High | 1,0 / 10000 | From 2.0 |
Mazanek | Low / high | High | 1,0 / 10000 | From 2.0 |
Schechtl | Low / high | High | 1,0 / 10000 | From 2.0 |
LGS-26 | High / high | Low | 0,7 / 10000 | About 32.0 |
Despite the many advantages, including high performance, factory models have some disadvantages, represented by a rather high cost and expensive training of personnel, as well as relatively expensive maintenance. Any homemade bending machine, as a rule, is easy to operate and available in manufacture, but their performance is poor.
Related video: do-it-yourself bending machine
https://www.youtube.com/embed/Rndk74cqR1Q https://www.youtube.com/embed/iA9IDpnB9eU
In general, relatively simple manual sheet bending machines are the most popular and most frequently sold types of sheet metal bending machines. They are distinguished by a simple design and easy operation; they will not require significant acquisition and maintenance costs. It is this option that can be performed independently, using a simple set of tools and materials that are quite affordable.