Soldering polypropylene pipes: an overview of the nuances of welding technology
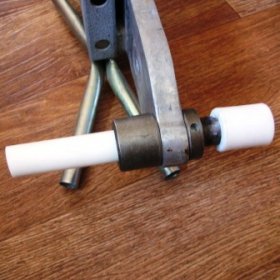
Plastic pipes, due to their affordable cost and ease of connection, have taken a leading position in the installation of water and even heating networks. Despite the fact that these structures are less strong and durable than metal, many prefer them, intending to change the utilities in their homes and apartments. Particularly attracted by the quick installation of products, since the soldering of polypropylene pipes allows you to create a strong and reliable connection in just a few minutes.
Classification of polypropylene pipes
Particularly strong plastic used for the production of pipes, is not subject to corrosion, resists the deposition of salts and the appearance of limescale. Polypropylene structures are designed for long-term operation. The manufacturer guarantees a 50 year service life of the facilities.
This is really possible provided that the pipelines are operated under the conditions of pressure and temperature specified in the instructions. Parts are designed for long-term exposure to high pressure at low temperature of the transported liquid and vice versa - high temperature of the liquid at low pressure.
Polypropylene pipes are available in four colors, which does not mean restrictions on use except black ones, which are made the most protected from UV radiation. Designs are used in water supply and heating systems; their connection with metal structures is possible. They can be used in all types of pipelines: open, closed and wall. Polypropylene pipes are divided into categories:
- PN 10 - version with thin walls. It is used for underfloor heating, whose temperature is not higher than 45 ° C or for distributing cold water.
- PN 16 - is used to organize cold water supply in high pressure systems or in low pressure heating pipelines.
- PN 20 - a universal pipe, can be used for both hot and cold water supply, where the temperature is not higher than 80 ° C.
- PN 25 - the structure is reinforced with aluminum foil. It is used for central heating and hot water supply with a temperature not higher than 95C. Can be used to connect a metal pipe to a plastic one.
Preparation for welding + process nuances
Guides that describe brazing technology indicate that structures with a diameter of less than 63 mm are usually joined by socket welding. At the joints of the pipes fittings are used, special connecting parts to which the elements are welded. Larger diameter pipes are joined without fittings by butt welding. This method is considered the most reliable for them.
Soldering of pipes made of polypropylene is carried out using a manual welding machine, which is popularly called an iron.For parts with a diameter of more than 40 mm, experts recommend using devices with centering devices that are somewhat more difficult to operate. The welding machines are equipped with special removable nozzles for pipes. They are heating elements made in the form of a sleeve for fusing the outer part of the pipe or mandrel for heating the inner surface of the part.
The diameters of the nozzles vary from 14 to 63 mm. The heating elements are coated with Teflon, a non-stick material. During the welding process, it is imperative to monitor the cleanliness of the nozzles and wipe them after each use with special scrapers made of wood or tarpaulin rags. This must be done while the elements are still hot, cleaning of cold parts is unacceptable.
Work procedure
The recommended technology for soldering polypropylene pipes involves several stages.
Stage # 1 - welding machine preparation
The appliance must be installed on a flat surface so that it is easily accessible. Before starting work, you need to determine which pipe diameters to be soldered and prepare the necessary heating elements. The design features of the device allow the use of several nozzles.
It is recommended that you install everything you need before warming up the appliance. The device heats up evenly, so the location of the heating element does not affect the temperature of the nozzle. They are fixed in the way that will be most convenient for work. Use special keys to install the nozzles. The desired temperature is set on the control panel of the device, for polypropylene pipes it is 260 °. The device turns on and heats up, which takes about 10-15 minutes.
At negative temperature values welding is prohibited. In addition, the soldering time of polypropylene pipes depends on the temperature in the room: in the heat it decreases, in the cold it increases.
Stage # 2 - pipe preparation
Using a pipe cutter or special scissors, the part is cut at a right angle. The cut point is cleaned and degreased with the fitting using a soap or alcohol solution. The details dry well. If work is carried out with pipes of the PN 10-20 grade, welding can be performed. If with PN 25, it is necessary to additionally clean the upper layers of aluminum and polypropylene. Work is carried out with the help of a shaver exactly but to the welding depth, which can be determined by the size of the nozzle of the welding machine.
Stage # 3 - heating parts
Elements are put on nozzles of the device of the necessary diameter. The pipe is inserted into the sleeve to the limiter, showing the welding depth, and the fitting is installed on the mandrel. The heating time of parts is strictly maintained. For each type of pipe it is different, the values can be found in a special table.
Stage # 4 - Welding Elements
The heated parts are removed from the apparatus and are connected with each other with confident fast movement in compliance with the alignments of the elements. Connecting parts they can not be rotated axially or bent. It is also necessary to strictly monitor that the pipe enters to a depth defined by the inner boundary of the fitting's socket.
Stage # 5 - cooling the connection
Preheated parts must be allowed to cool, this is especially important for thin-walled pipes. Any deformation of parts at this time is unacceptable, they can lead to sealing of the inner lumen of the pipe. After the parts have cooled completely, it is necessary to blow or pass water through them to make sure that they are passable.
Video example of soldering work
Also, the whole process can be observed in this video instruction:
Recommendations on how to solder pipes made of polypropylene are quite simple. You can cope with this work yourself.Experienced welders offer beginners to solder the first part, cool it and cut it to make sure that everything is done correctly. If there are errors, they will be immediately noticeable. Thus, you can quickly learn how to make reliable connections of polypropylene pipes, which will certainly come in handy during installation or repair of pipelines.
2 comments