Fire, water and copper pipes: features of work with copper pipes and fittings
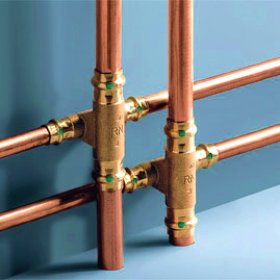
The range of materials for arranging pipelines is constantly expanding. Among other products, modern plastic parts are confidently leading in terms of attractive performance and low price. Despite this, traditional copper pipes and fittings do not give up their positions and remain highly demanded material for highways of various purposes. According to GOSTs, copper pipes can be used in various sectors of the economy. This is due to the characteristics of the metal and special technology that allows you to get seamless products.
Content
Varieties of copper products
There are several classifications of copper pipes. Let's consider some of them. According to the manufacturing method, the products are distinguished:
- Unburnt. They are made of pure metal by stamping or rolling. They are characterized by high tensile strength, which is about 450 MPa. At the same time, the ductility of the metal decreases, which creates certain limitations when using parts.
- Annealed. Differ in special processing technology. The pipes are heated to 700C and then gradually cooled. As a result, products somewhat lose their strength, but become more ductile. Such pipes stretch perfectly, just before the gap, the length of the element can increase one and a half times. Annealed products are softer, which simplifies their installation.
The shape of the section distinguishes between round and rectangular elements. The latter are distinguished by a higher cost, which is due to the complexity of their manufacture. Used for the manufacture of conductors in the stator windings of electrical equipment, cooled by a liquid method. The sizes of non-insulated copper products in outer diameter vary from 12 to 267 mm. In addition, each of the sizes may have a different wall thickness, which is in the range from 0.6 to 3 mm. For gas supply, products with a minimum thickness of 1 mm are used. In plumbing, sizes 22, 18, 15, 12 per 1 mm, 52 by 2 mm and 42, 35, 28 by 1.5 mm are most often used.
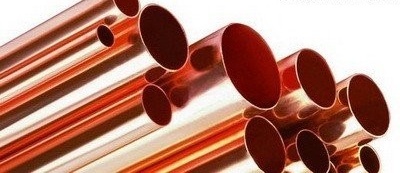
Annealed copper pipes lose some strength, but they acquire special ductility and softness, which facilitates the process of their installation
GOST 52318-2005 regulates the manufacture of copper parts in three types, differing in degree of hardness, operational and mechanical properties:
- Soft. Designated by M or W, obsolete r or F22. Withstand the distribution without cracks and tears in the process of increasing the outer diameter by 25%. Can be subjected to bending and fitting-free connection "cold".Products are used to equip heating and water supply systems with a radial distribution of connections to heating and plumbing fixtures, as well as for heat pumps, floor, as well as panel heating.
- Semi-solid. Marking P or LV, obsolete version z. Parts withstand distribution in the process of increasing the diameter of the pipe by 15%. Less ductility than soft products requires the use of heat for a fitting-less joint. For bending, a pipe bender is required.
- Solid. Designation T or H, obsolete z6 or F30. During installation, pipe distribution takes place only during heating. A pipe bender is used to bend the part. Solid, as well as semi-solid, elements are used to equip highways without frequent changes in direction and turns. In addition, such products are used for pipelines for which increased mechanical strength is required.
Some manufacturers produce special pipes with additional options that are in demand for heating and water supply systems:
- With insulation polyethylene thin-walled shell, the thickness of which is 2-2.5 mm. The material is resistant to chemical and mechanical influences, is applied to pipes whose diameter is from 12 to 54 mm. The casing reduces heat loss present in heating systems and prevents the occurrence of condensation on cold water pipes.
- With protective insulation from 2.5 to 3 mm thick. The inner side of the polyethylene shell is equipped with small longitudinal teeth forming air channels. Thus, the thermal insulation characteristics are improved, and it becomes possible to carry out the thermal expansion of the monolithic pipe under temperature fluctuations.
- With foam insulation: synthetic rubber, polyethylene foam, soft polyurethane foam, etc. The width of the insulating layer may exceed 30 mm. The shell is used to reduce high heat transfer in hot water and heating systems.
If necessary, you can purchase special parts for shelter and thermal insulation of mounted pipelines.
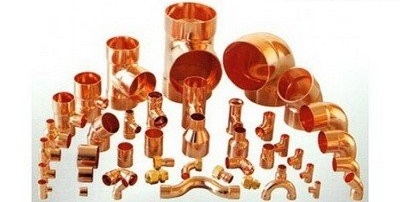
Fittings are used to connect copper parts. Their range is very wide. They vary in shape and are intended for the implementation of various types of compounds
Why are copper pipes better than pipes of other materials?
Copper parts are excellent for transporting various media, due to the unique combination of material properties:
- Resistance to temperature differences. The copper pipeline maintains the temperature of the heat carrier in the range from -200C to + 250C. There are no restrictions on exposure time or pressure.
- High strength and ductility, which when exposed to negative temperatures do not decrease, but increase. This makes it possible to transport non-freezing gases or liquids in winter conditions.
- Resistance to corrosion, the damaging effects of ultraviolet radiation and chemical compounds, which ensures a long service life of pipelines.
- High strength and ductility make it possible to produce pipes with a wall thickness of 1.5 to 3 times less than that of steel or plastic products. Copper parts are quite easy to process and bend, including manually.
- Low roughness coefficient, which is lower than that of plastic. This makes it possible to use smaller internal diameters and increases the throughput of the pipeline.
- Bacteriostatic or the ability to restrain the development and growth of microflora, which allows for increased infectious safety.
- Reusable. When replacing or eliminating a copper pipe, pipes can be reused. In addition, the products are recyclable.
- Attractive appearance of the parts, which allows them to be used as an element of room decor with open laying.
The main disadvantage of copper products is their high cost, which, however, pays off for many years of trouble-free operation.
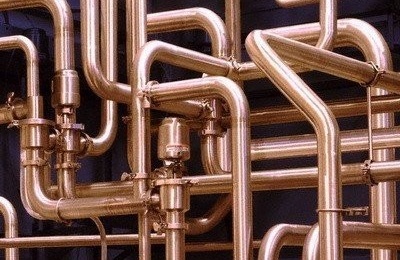
Copper pipes are very ductile and durable. Using various fittings from them, it is possible to assemble a pipeline of very different, even very complex configurations
What fittings are on the market?
Copper pipelines are quite simple and easy to install. This is due to the presence of a large number of types of connections and fittings for them, which makes it possible to carry out systems of complex configuration. When carrying out installation work, bulky special equipment is not required. Connections in copper pipelines are considered the most reliable elements. Several types of fittings are distinguished depending on the connection method used.
Option # 1 - compression elements
Parts are equipped with a special crimp ring, which ensures the tightness of the connection and secures the fitting to the pipe. The element is hand-tightened with a union nut and wrench. The main advantage of compression parts is ease of installation. Special equipment and heating are not required. Using this method, you can mount the pipeline in the most inaccessible places. The labor costs for installation are small, and the resulting system is quite durable and tight. Crimp fittings also have disadvantages. They are not designed for high pressure, they need to be periodically monitored and tightened. Such details cannot be concreted.
Theoretically, compression elements provide a collapsible connection. However, practice shows that after the first disassembly and assembly, the reliability of the unit decreases sharply and it has to be changed. Two types of crimp fittings are distinguished. They are marked with letters A and B.
- Parts A are used for onshore pipelines made of semi-solid grades of copper.
- Details B are used for arranging ground and underground utilities from pipes made from semi-solid and soft grades of metal.
Installation of parts of both types is carried out according to a similar scheme.
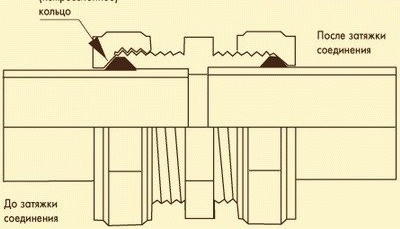
The diagram shows a compression fitting device. It is easy to install, but does not provide a strong enough connection that needs regular monitoring
Option # 2 - Capillary Fittings
Capillary brass fittings are called copper fittings. They connect the pipes using solder, that is, copper, tin or silver wire, located under the internal thread of the part. During installation, the fitting is put on a pipe that is precoated with flux. The connection area is heated with a torch until the metal solder melts and fills a small gap between the fitting and the pipe. After which the details make it possible to cool. Then external cleaning is carried out using a special tool. The pipe is ready for use.
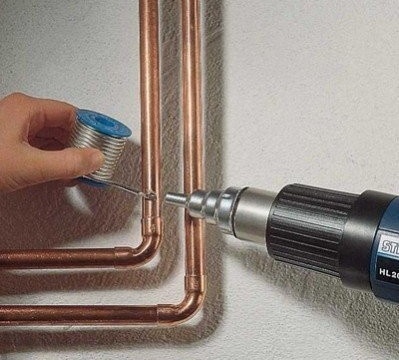
The soldering process of the fitting involves the use of solder, which melts to fill the gap between the parts
The advantage of this method of connection can be considered high reliability. The maximum operating pressure of the unit is 40 bar at a system temperature of 150 ° C. The capillary method gives a very even and accurate seam, during the work a minimal amount of solder is used, the cost of installation works is quite democratic. The relative disadvantages of the method include the mandatory presence of a burner and the need for a certain qualification and experience for the person who will be involved in the installation.
Option # 3 - Press Fittings
The principle of operation of parts is based on the use of the ductility of copper and its susceptibility to deformations that are created by mechanical stresses.To obtain such a connection, the pipe, which is previously inserted into the press fitting, is crimped with press tongs. Minimum crimp deformation force 32 kN. This allows you to create an all-in-one strong connection. A sealing ring is laid along the contour of the press fitting, which ensures tightness of the connection. The connecting part can be rotated, tightness and strength do not suffer from this. Structurally, press fittings differ on parts with double and single contour of deformation compression.
The main advantage of these elements is the possibility of quick installation without the use of electric heaters or an open flame. They are installed at facilities where the use of open flame burners is prohibited, as well as inside various tanks, tanks and containers. The resulting joint is more durable than that made using compression parts. The disadvantages of the elements include a higher cost than solder fittings, and the need to use special equipment during installation - hydraulic or electric presses with a set of tongs of different profiles and diameters.
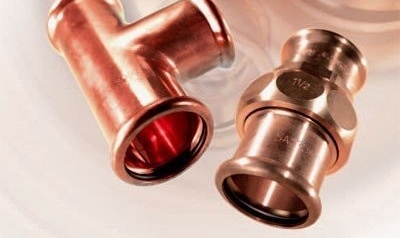
Installation of press fittings will require the use of an electric or hydraulic press with a set of pliers of different diameters and shapes
Features of connecting copper pipes
When designing communications from copper parts, you need to know that to create a durable pipeline, only homogeneous materials are used: copper and its alloys. If this is not possible, adhere to the following rules:
- The connection of unalloyed galvanized and unalloyed steel with copper is prohibited. In this case, electrochemical processes are activated that accelerate the corrosion of steel elements.
- The connection of copper with acid-resistant steel is allowed.
In general, a combination of steel and copper pipes is highly undesirable. If it is impossible to avoid such connections, it is best to perform them like this: first, steel elements are mounted, after them - copper.
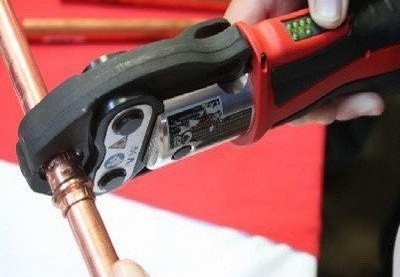
Combining steel and copper piping is strongly discouraged. If this cannot be avoided, experts advise installing a copper section only after steel
You can learn more about soldering from the article *Soldering copper pipes - an overview of common mistakes and the right technology*.
And here's how to bend a copper pipe:
Copper pipelines are very reliable and durable. It does not matter if they are equipped with a hidden or open method, they will last as long as the building itself, where the products are laid. A wide range of fittings allows you to equip communications of various configurations, using the most convenient method in this case. The relatively small distribution of copper products is explained by their high price. The cost of a copper pipeline will be significantly different from the price of a plastic analog. However, those who decide to install copper communications will not regret their decision, having received a strong, trouble-free and durable system.