Installation of HDPE pipes: welding, coupling connection + how to bend / straighten such a pipe
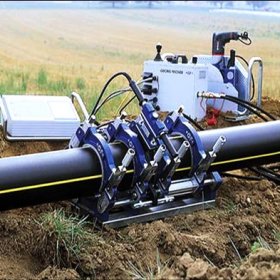
Housing of modern man is almost impossible to imagine without polymers. Especially popular was low-pressure polyethylene, which occupied a significant sector in the plumbing equipment market. Today, most of the pipelines are produced from it, through which various media are transported, as well as pipeline fittings to them. HDPE pipes have become popular due to their undeniable advantages, as well as simple installation - it can be performed by a person without special training. But, as in any business, there are some peculiarities and nuances here, so it’s not a hindrance for a beginner to begin to learn how to properly install pipes with their own hands. Read this article, that's what this is about.
Content
Characteristic and scope of HDPE pipes
HDPE pipes are made of high-quality dense polyethylene and are durable and flexible, have a low weight, and therefore are easy to install. They do not need a cathode coating like metal pipes and do not require special maintenance. Their main advantages:
- they do not rot, are not subject to corrosion, are not afraid of hostile environment;
- high wear resistance (the term of their operation is more than 50 years);
- flexible, do not crack at low temperatures or when water freezes inside them;
- environmentally friendly;
- not exposed to harmful effects of fungi and bacteria;
- can be used in seismically active areas;
- relatively inexpensive.
Due to its many advantages, HDPE pipes are widely used in the construction industry. They are used:
- for installation of sewer systems;
- for assembly of a water supply system;
- when laying electrical networks - to protect cables (in the form of smooth or corrugated pipes);
- during the construction of artesian wells;
- in irrigation systems in agriculture.
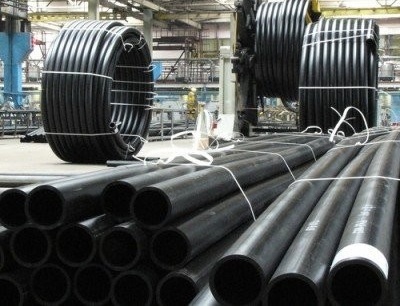
HDPE pipes are widely used both in industry (hydro and gas pipelines), and in everyday life (sewage, water supply)
Unfortunately, polyethylene pipes cannot be used for heating and hot water supply, since the temperature of the transported liquid should not exceed + 40 ° С. These restrictions are caused by the fact that polyethylene begins to soften already at + 80 ° C.
The popularity of polyethylene pipes is due primarily to the ease of installation. They are connected in several ways.
You can find out more about the characteristics of HDPE pipes in our next material:https://aquatech.tomathouse.com/en/ehlektrosnabzhenie/truba-pvh-dlya-elektroprovodki.html.
Pipe Connection Methods
PND pipe connections are of two types:
- one-piece (butt-weld and electrofusion welding);
- detachable (using connecting parts).
One-piece connections
usually used in areas where the pipes are to work in the field of high pressures. Weld joints are suitable for all HDPE pipes with diameters greater than 50 millimeters. The weld obtained as a result of welding is several times stronger than the pipe itself and provides absolute joint sealing.
Butt welding
Butt welding of pipes PND is carried out using a special apparatus. The essence of this connection is to heat the ends of the pipes with a special heating element to a viscous state. The softened ends of the pipes are joined under pressure and the joint is allowed to cool naturally. Previously, the ends of the pipes are degreased and cleaned of impurities.
Note! During operation, it is necessary to monitor the heating time, the height of the melting of the material, the pressure on the abutting surfaces and that the heating temperature is maintained in the desired mode.
Received Weld should be even, the height of its protrusion is the same. Only in this case will it be as durable and reliable as possible.
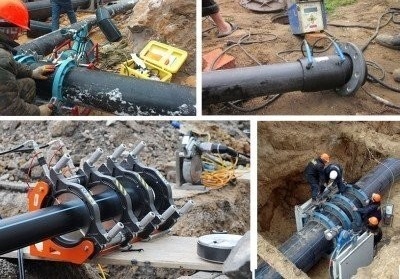
Butt welding is the main way to connect HDPE pipes. With strict adherence to welding technology, strong and durable joints are obtained.
Butt welding is considered one of the most popular ways to connect pipelines, but you can not discount the second, no less effective way - connection using electric couplings.
You may also find useful material about the types of welding machines, their pros and cons:https://aquatech.tomathouse.com/en/uchebnik/oborudovanie/svarochnyiy-apparat.html.
Electrofusion welding
For this type of welding, a molded polyethylene coupling is used. Electric spirals are inserted into it, and when electric current passes through them, the coupling is heated to the desired temperature and welded to the pipes, fastening them firmly when solidifying. As with butt welding, before starting work, the ends of the pipes are thoroughly cleaned.
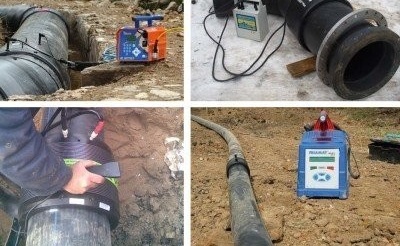
Electrofusion welding technology is actively used in cramped conditions - when creating inserts in previously connected pipes, in wells, during repair and installation of bends, etc.
Attention! A prerequisite for the process of electrofusion welding is to ensure the immobility of the parts during heating and cooling.
Welded joints must meet the following requirements:
- the offset of the welded segments in relation to each other should not exceed 10% of the wall thickness of the polymer pipe;
- the butt weld should not be located below the external level of the pipe surface;
- a high-quality weld has a roller height of not more than 2.5 millimeters on pipes with a wall thickness of up to 5 millimeters, and on thick-walled pipes whose wall thickness is 6-20 mm, its height should not be more than 5 millimeters.
Detachable connections
This type of connection is carried out in areas where reconstruction or repair may be required in the future and there will be a need for disassembly. This is found in private households when you need to connect a pipe from a water source to a section of the water supply leading to the house.
There are also situations when it is impossible to apply the welding method (there is no necessary equipment or the connection needs to be done in water). In such cases, a sleeve connection is used. Couplings specially manufactured for HDPE pipes reliably fasten abutting segments.
The detachable connection of pipes is carried out in two ways:
- bell-shaped connection (using elastic gaskets);
- flange and fitting connection, for which special fasteners are used.
To assemble the mounted parts, there is no need for tools and devices, except for a special wrench, with which help unscrew and tighten the clamping nuts on the connecting fittings. This method is suitable for joining pipes of small diameter (20-35 mm).
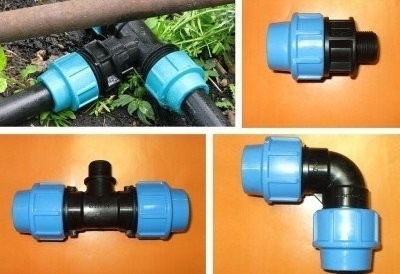
The use of compression fittings makes it possible to connect HDPE pipes without using a welding machine - their installation is carried out by assembling the fitting elements with a threaded method
The advantage of compression fittings is the ability to disassemble mounted parts if necessary, and you can do this repeatedly and even a person without special training can do this work. In addition, this type of installation can be performed even at very low temperatures, and the sale of a wide range of connecting elements of various diameters allows you to collect any necessary wiring and branching in the pipeline.
How to straighten or bend the HDPE pipe?
Polyethylene pipes are sold in straight sections (12m) or in bays, on which several hundred meters are wound. If necessary, you can rewind the necessary part of the pipe from the coil and cut it off, but the question is how to straighten the HDPE pipe wound with rings so as not to spoil it?
If the construction or replacement of the pipeline is carried out in the summer, it is best to leave a bent pipe to lie in the sun. UV is not afraid of polyethylene, but under warm summer rays the pipe softens a little and then it can be easily laid in a trench or fixed along the wall. In case of emergency replacement of the water supply system in winter, the pipe can be heated with hot water. Often all sorts of improvised tools are used, such as brickwork, metal railings, etc. The shorter the straightened pipe section, the easier it is to straighten it to the desired state.
When installing pipelines, the opposite situation often arises when you need to know how to bend the HDPE pipe correctly so as not to damage it. Use brute force is not worth it. To do this, pour boiling water over the place of the supposed bend of the pipe or warm the bend at the place with a construction hairdryer or gas burner.
Attention! With insufficient heating, the pipe may break when bent, and if the heating device is too close to it, the polymer may ignite and this will also lead to damage to the product.
Pay attention to the instructions for inserting into a plastic pipe without welding:https://aquatech.tomathouse.com/en/uchebnik/truby/vrezka-v-plastikovuyu-trubu-bez-svarki.html
When choosing a method for connecting pipes, it is important to consider the operating conditions of the future pipeline (which medium will be transported, pressure in the pipeline, pipe diameter, etc.). The reliability and durability of the pipeline system will depend on the correct choice and quality of the connection.
2 comments