How to make a filter for a well with your own hands - the device of 4 home-made designs
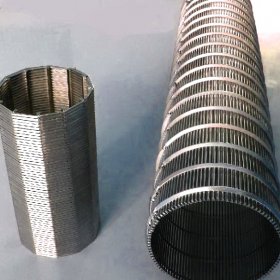
Water is the basis of life on the planet. It is extremely difficult for a person seriously spoiled by the benefits of civilization to do without it. Those who are going to live in a summer cottage or build a house in the country are trying to equip an autonomous water supply system. A fairly common problem for such structures is blockage of the well, which is the basis of the structure. It becomes an urgent need to use a filter for the well: to make it with your own hands is quite simple.
A filter is a section of a casing working zone. It should prevent the ingress of sufficiently large particles into the structure, while clean water flows unhindered into the column. In addition, the filter is an additional protection of the barrel walls against possible collapse. The design consists of three significant parts: the filter itself, the superfilter section and the sump, in which large rock particles accumulate.
Content
Perforated Hole Filters
One of the most common systems are hole filters. They are a regular pipe with perforation applied to its surface. Despite the apparent simplicity of the design, they have pretty good performance. Therefore, many of those who are considering how to make a filter for a well choose this option.
One of the main advantages of the system is ease of manufacture and low cost. Such designs are used for different types of rocks, most often installed in artesian wells with low head and unstable aquifer.
The hole filter can be made by yourself. This will require a steel pipe of the desired diameter, preferably from an exploration or oil assortment. If you choose plastic, which is also possible, you need to take one that is safe for the human body. Further, the diameter of the drill for perforation is selected according to the size of the holes. The size of the holes depends on the particle size distribution of the rock.
The manufacturing process takes place in several stages:
- The length of the sump is measured. The pipe is laid on a horizontal surface and marked on it. It should be borne in mind that the perforated section must be at least 25% of the length of the entire pipe and subsequently located on the water intake section of the well.
- Drilling holes. At least 100 cm usually recedes from the edge, where the first element is executed. The interval between them should be about 1-2 cm, and the holes are staggered. It is advisable to drill them at a certain angle, preferably 30-60 °, in the direction from bottom to top.At the end of the work, all sharp edges are cleaned, the pipe is lifted and carefully tapped to remove all chips from the holes.
- The lower part of the pipe is closed with an ordinary wooden cork. For better protection, a mesh for a well filter is applied to the structure to protect the holes from clogging.
Slotted Filter Designs
Along with hole filters, slotted systems are used in fractured and rock-prone rocks. They are more preferable in their design, since they have a larger than perforated throughput. There are no “dead” zones on their surface, and the area of one slot is one hundred times greater than the area of the hole.
The main drawback of the structure is considered to be lower bending strength, therefore, in the manufacture of the so-called "stiffening belts" - continuous sections without perforation are necessarily provided.
To make a slotted filter for a well yourself, you will need to prepare a pipe and a milling tool or gas cutter, depending on how the holes are made. The dimensions of the width of the slots based on the composition of the rock can vary from 3 to 5 mm, lengths from 25 to 75 mm. Holes are located both in waist and in checkerboard pattern. A metal mesh can be applied on top.
Grid selection is quite simple. It can be square or galloon weaving. Experience shows that the best strength and permeability of a brass grid of brass weaving. Choosing the size of the holes is also easy. To do this, dry sand is sifted through several nets. Choose one that misses, on average, about half. However, for particularly fine sands, the option that missed about 70% is quite suitable, and for large fractions - 25%.
Proper manufacture of a filter for a well involves the determination of sand sizes in order to select the grid as accurately as possible. You can do this yourself by sprinkling some dry sand on graph paper. Particles with a size of 0.5 to 1 mm are considered large, medium - from 0.25 to 0.5 mm, and small - from 0.1 to 0.25 mm. Galloon weaving nets have a special marking in the form of fractions. The numerator indicates the number of wires in the base, in the denominator - in the weft, based on a square measuring 25x25 mm. If the filter will work with gravel, then the grid is selected only with square weaving.
Before applying the mesh, a stainless steel wire is spirally wound onto the filter with a pitch of 15-25 mm. The diameter of the wire is 3 mm. Every 0.5 m along the length of the frame, it is soldered pointwise, providing maximum strength. The lap mesh is put on the pipe and pulled together in a spiral wire. Pitch - 50-100 mm. Each twist after twisting is bent under the screed with pliers. You can also solder the mesh. To do this, first attach one edge, and then overlap on it - the second. In this way, you can independently produce the best filter for the well on the sand, which is considered a slotted design with a mesh.
Filter wire systems
The wire filter is a special wire with a special profile wound around the frame. This option is preferable to hole and slotted filters with a mesh, because the thickness of the wire is much larger, which ensures a longer service life. A quality filter should be welded at all points of contact with the frame. Its throughput directly depends on the shape of the cross section and the pitch of the wire. Thinking about how to make a filter for a well yourself, this option is hardly worth considering, since this is an almost impossible task.
However, those who are not afraid of difficulties can still try to make a wire filter. Its frame is a slotted design, the size of the holes of which should be equal to the average diameter of the rock particles. Before winding, 10-12 longitudinal rods with a diameter of at least 5 mm are superimposed on the frame.
Then, stainless steel wire, diameter 2-2.5 mm, is wound under tension on the base. It is better to perform the operation on a lathe, but it can also be done manually, then the operation will require special patience and accuracy.
Gravel filtration plant
The gravel filter is a fairly simple design that allows the well to function efficiently. The construction is being arranged in clayed and fine sands. To create a gravel filter, a hole for a well larger than the diameter is drilled. Gravel, which before this is carefully selected and even calibrated, since it is a one-dimensional fraction that is required, is poured into the well from the mouth. When choosing gravel, you need to consider the average particle size of the rock: they should be 5-10 times smaller on average. Spraying thickness - not less than 50 mm.
Thus, a home-made filter for a well is quite real. The main thing is to correctly calculate your own strengths and choose the most suitable option. Careful adherence to the instructions and the right material will allow you to collect a good filter, not inferior in quality to those that can be bought in the store.