How to make a brick and metal stove for a bath
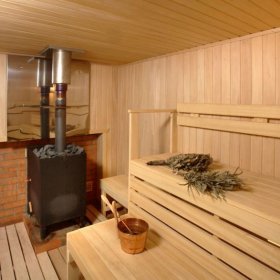
The stove is the central element of the bathhouse - many try to make it on their own. This decision is fully justified: it is not easy to select a factory version for the individual characteristics of the object. Consider the criteria that a bath stove must meet, as well as how to make it yourself with bricks and rolled steel.
Content
Design features of the furnace for the bath
At first glance, a bath stove differs from a heating stove only in the presence of a backfill of stones - a heater, and the mandatory presence of a hot water tank. But there are unobvious differences.
To shift the maximum heat generation towards IR radiation, you need a material with high heat capacity, but low heat conductivity. The stone filling also possesses such properties.
The sauna furnace has higher requirements for the tightness of the body. The fact is that in heated air the harmful effect of carbon monoxide is amplified, so it is very important to completely eliminate its ingress into the steam room.
If you want to be able to heat the furnace during the adoption of bath procedures, the loading door of the furnace along with the blower must be brought to the next room. If this is not done, then during the firebox in the steam room the oxygen concentration will drop and people will begin to suffer from suffocation.
Varieties and recommendations for selection
The material of the furnace primarily depends on the volume of the bath. Consider several options:
- A spacious building with several rooms requires a brick oven, which is able to give off heat for a long time.
- The steam room is modest in size with a volume of 30 to 35 m3 You can install a cast iron stove.
- For a bath with the most compact dimensions, a steel oven is also suitable.
Of no less importance is the material from which the walls of the bath are made. Felling from birch or linden is called light, from oak - heavy. These terms should not be taken literally: the word "heavy" in this case does not mean weight, but the presence of tannins in the wood. People with poor health, as well as women and children, are not recommended to bathe in such saunas.
Table: power and weight of stones for linden, birch and oak baths
Type of bath (ceiling height from 2.2 to 2.4 m) | Power (kW / m3) | Weight of stones (kg / m3) |
Linden tree | 0,5 | 2,7 |
Birch | 0,7 | from 3.6 to 4 |
Oak | 1,2 | 6 |
According to the method of heating stone filling, bath stoves are divided into two varieties.
Flowing stoves
In such furnaces, the heater does not separate from the furnace with an impenetrable barrier, so flue gases seep through it before entering the chimney.
Thanks to this decision, the stones warm up extremely quickly, but you have to put up with some disadvantages:
- Complicated furnace design.
- With some periodicity, the stones have to be cleaned of soot.
- Pressing (pouring water or kvass on the stones) is possible only after the fuel has completely burned out.
- You can use only fuel that produces a small amount of carbon deposits (pellets, aspen, etc.).
With a deaf heater
In this embodiment, the stones are fenced off from the furnace and gas duct with a stove. In terms of advantages and disadvantages, the situation is reversed: the heater is heated for a long time, but it does not need to be cleaned and can be used to produce steam at any time.
In order for the stones in the dead stove to heat up sufficiently, two conditions must be met:
- the furnace should be metal (the thermal conductivity of the brick partition will not be enough);
- have a capacity of not more than 25 kW (the bath should consist of one room with a volume of up to 45 cubic meters).
With increasing power of the furnace, its size grows, and the contact area of the heater with the partition, in accordance with the law of the square-cube, does not “keep pace” with its volume.
It should be borne in mind that the ceiling height in a steam room with a blind heater should not exceed 2.2 m, otherwise instead of light steam it can turn out to be heavy.
Of all these options, only a steel furnace is available for independent manufacture at an amateur level. Brick can also be built at home, but in view of the difficult operating conditions, only an experienced stove-maker can do this. Cast iron bath stoves are made only in the factory.
Metal furnace
In everyday life, the proposed here version of the sauna heater is called a “quick oven”. This name is well-deserved: it will be possible to use the steam room within 1.5–2 hours after the start of kindling. This advantage is due to the use of a flow-type heater.
The furnace is designed for a bath with a steam room up to 25 cubic meters. m - an option for periodic use by a family of 3-4 people. For operation in a larger building, lining with fireclay bricks is required.
Necessary materials and tools
It will take steel. We will use the most affordable steel - structural (it is also called "black" in everyday life), with a low carbon content (any grade up to Steel 20 will do). High-carbon grades like Steel 35 or Steel 45 are hardened and embrittled by high temperature exposure.
Here is what kind of rental should be obtained:
- A section of pipe with a diameter of 520–700 mm and a length of 1600 mm. Of course, the furnace body can be made welded, but being made of a single piece of pipe, it will be more durable and durable. The wall thickness of the workpiece should be 7–10 mm.
- A pipe with a wall thickness of 5 mm and a diameter of 100–120 mm is a blank for the chimney.
- A cut of a sheet of 2.2x1 m format with a thickness of 10 mm or more.
- A rod with a diameter of about 10 mm.
You will also need a number of products:
- Factory-made grate. The most durable are products made of cast iron by casting. But for lack of a purchased option, you can weld such a grid from a steel bar.
- Hinges for doors - only 8 pcs.
- Heck for doors - only 3 pcs.
- Valve or ball valve.
Tools used in the work:
- grinder with cutting and cleaning circles;
- apparatus for electric welding;
- scissors for metal.
Step-by-step manufacturing instructions
- The blank for the body (pipe length 1600 mm) should be cut into two parts - with a length of 900 and 700 mm.
- In the lower part of the workpiece with a length of 900 mm, it is necessary to carefully cut a rectangular hole of 200x50 mm in size, which will serve as a basement. It should be located 70-100 mm from the end. It is important not to damage the cut out part of the wall - subsequently a door will be made of it.
- A little higher, in the same way, it is necessary to make an opening for loading fuel.
- Cut rectangular fragments into doors. To do this, it is enough to weld the heck and halves of the loops to them.
- Having welded the mating parts of the hinges and hooks to fix the locks to the case, you can install the doors in place.
- Now you need to make a flat ring on which the grate will be laid. It should be cut from a steel sheet 10 mm thick. The width of the ring is selected taking into account the dimensions of the grate, and its diameter should be equal to the inner diameter of the casing.
Tip. Cutting blanks, especially those with rounded contours, is best ordered in a specialized workshop or at the metal depot where the rental is purchased. If you take up this business yourself, you will not be able to save a lot, as you will have to buy several circles for the grinder. It will take a lot of time to “bring to mind” the rounded edges, because after cutting with a grinder they always turn out to be angular.
Next, a grid should be welded from the rod, on which the stones will be laid. The step between the bars is selected in accordance with the size of the stones - they should not fail. Having welded the grate into place, stones are laid on it.
From the sheet, it is necessary to cut a round lid for the furnace, to which a chimney is welded with a certain offset from the center. In the lid, of course, you must first cut a hole to remove smoke. The lid is welded on top of the stove so that the chimney is closer to the back of the stove.
Another circle of the same diameter must be welded below as a bottom.
Note. You can leave the furnace without a bottom, and in the process of inserting a wide and shallow container under it, it will be easier to remove the ash.
We weld a water tank on top of the furnace, the role of which will be played by the remaining pipe segment of 700 mm in length. The chimney inside it will act as a heater.
At the bottom, a fitting with a thread must be welded into the tank wall, onto which a tap or valve will subsequently be screwed.
The final stage is the manufacture and installation of the lid for the water tank. It is done in several stages:
- a circle should be cut from the sheet with a diameter corresponding to the diameter of the furnace body;
- the circle must be cut along the chord into two parts, the smaller of which will play the role of a hinged hatch;
- in a large workpiece, a hole is cut out for the chimney, after which it is welded to the top of the water tank;
- a small workpiece, that is, a hatch, is fixed to the tank lid with hinges.
At this, the manufacture of a steel furnace for a bath can be considered complete. Note that the construction proposed here is far from the only possible option. The figure shows several more furnaces made of rolled steel.
Brick option
Now consider the technology of creating a brick sauna stove.
For the purpose of speedy warming up, it will also have a flowing heater.
Once again, let us draw the reader’s attention to the fact that it is better to entrust the construction of this structure to a master with sufficient experience in the furnace business - this is due to particularly difficult operating conditions and increased safety requirements.
Materials
Significant heat loads and the need to make the walls of the furnace absolutely airtight determine the highest requirements for the quality of materials.
The internal walls of the structure, which will have to come in contact with fire and incandescent combustion products, should be laid out of fireclay bricks. In order, it will be indicated in yellow. You cannot break bricks into pieces or grind them with a grinder - all blocks in ½ or ¾ of the brick should be purchased ready-made (they should have only smooth edges).
The clay and sand solution used should be of medium fat content. Clay and sand are usually mixed in a 1: 1 ratio. Sand should be used without organic impurities - mountain or ravine. It can be recognized by the silver color and the angularity of the granules. Microcracks will quickly appear in the solution mixed on river sand with rounded granules, as a result of which poisonous carbon monoxide will begin to flow into the steam room. Sand should be sieved through a sieve with a mesh size of 0.15-0.25 mm, washed and calcined.
Tip. If the available clay turned out to be too oily, dilute it with ground clay brick.
For cladding, use front brick with smooth edges and rounded edges.
Masonry
Work on the construction of the furnace is performed sequentially.
Foundation device
In the soil on a sandy bedding, it is necessary to fill in a reinforced concrete foundation, the edges of which should protrude beyond the outline of the furnace by at least 50 mm on each side. Sand filling is necessary - without it, the furnace will be unstable. The depth of the foundation sole depends on the presence of heating in the room: if it is (or the bath is heated every day), it is enough to go deep by 400-600 mm; in the absence of heating, in combination with the rare use of the bath, it is necessary to immerse the foundation to the depth of freezing of the soil.
In the upper part of the foundation, you can leave a cavity - this is a cistern in which inventory is usually stored. Overlapping for it can be reinforced concrete beams, a steel sheet or a brick arch laid on top of wooden beams or rolled steel.
Intermediate row
A waterproofing coating consisting of two layers of roofing material is laid over the reinforced concrete foundation.Instead, you can lay a steel sheet, and on top of it - basalt cardboard with a thickness of 4-6 mm.
Next, lay out an intermediate brick row. With its help, the unevenness of the foundation is compensated, so that in the end the surface of the row becomes perfectly flat and strictly horizontal. In addition, in plan, this part of the furnace should be a perfect rectangle. This is checked by measuring the length of the diagonals - they must be equal. The solution when laying the first row is not used.
Another layer of roofing material is laid on top of the bricks.
Fire protection
To exclude ignition of the wooden wall of the bath, a brick wall 5 rows high is erected between it and the stove. Used brick of medium quality and the usual building cement-sand mortar.
Furnace body
Subsequently, the bricks are laid row by row according to the order.
The thickness of the joints in the chamotte masonry should be 3 mm, between the facing and chamotte bricks - from 6 to 10 mm. The same wide seams should be left between the brick (any) and metal products. It is quite difficult to apply the solution with a thin layer using a trowel, so this is usually done with your hands. Bricks need to be laid exactly - right in their place. You cannot correct or tap the block - if it lay crooked, you need to shift it over a new one, re-applying the solution.
Experienced stove recommendations
Doors are most conveniently fixed using galvanized wire with a diameter of 2 or 3 mm. When installing the door blew (on the 1st row), the wire must be folded in half before twisting. A more powerful harness will be needed for the furnace door - three pieces of wire folded in half are used here (the thin one will quickly burn out).
Tip. To make it easier to bend a thick wire, it needs to be slightly burned.
Wire twists must be laid in grooves specially cut in bricks.
The frame of each door should be wrapped with asbestos cord in two layers. It plays the role of a sealant and at the same time a temperature seam - it allows cast iron to freely increase in volume when heated.
In height, the door usually does not fit between the brick rows, so the bricks that overlap it have to be cut. It is important not to forget: the thickness of the asbestos cord with which the door frame will be wrapped should be taken into account.
Note. Since the blowing door, which allows access to the ash chamber, does not heat up too much, it is allowed to put it on the solution.
The dimensions of the grate should be less than the internal dimensions of the furnace by at least 10 mm - then there will remain a gap of 5 mm between it and the brick. If this rule is not observed, the grill deforms the masonry when heated.
Note. Sometimes, due to deviations in the size of the bricks, the shelf on which the grate should lie cannot be made strictly horizontal - the face of a brick is below the plane of the entire row. Most often, this happens with bricks mounted on spoons. The difference in height must be compensated with plates cut out of brick.
In the 5th and 7th rows, again, due to deviations in the size of the bricks, between the two of them located at the back wall, too wide a seam may form. This cannot be allowed, because then the clay-sand mortar will quickly crumble here. In this case, both bricks should be shifted to the side of the blower by 3 cm, while reducing the seam between them to a minimum size, and instead of the 3rd brick, lay two bars. Their width is selected so that the seam between them is almost absent. The left bar moves 1.5 cm toward the front wall.
The water tank at the junction with the bricks should be twice wrapped with asbestos cord. On the one hand, this will eliminate the burning of its walls in the event of a kindling of a furnace without water, on the other hand, it will reduce the rate of water heating, without which it would boil even before the steam room was completely heated.
The slab is installed on top of the 9th row so that it lies on the bricks with a gap of 2–2.5 cm.
The stove grill can be welded from steel channels. The ideal option is rails that have already been used for their intended purpose (their surface is hardened thanks to hardening).
Stones should be laid after the oven is dried and warmed up by an accelerating firebox.
Drying the oven lasts at least 2 weeks. The optimum temperature is 20-30 degrees, so it is better to build a furnace in the summer. When it dries, it is necessary to produce a 5-fold accelerating firebox with interruptions of 12 hours. The fuel used for this must be of high quality - aspen logs or pellets are best suited. Start with a small portion - up to 5 kg. With each subsequent “acceleration”, the mass of fuel gradually increases, bringing to the last firebox to the maximum.
Chimney
In the chimney of a sauna stove, two sections are distinguished. The first section is that part of the pipe that connects directly to the furnace and is located inside the steam room. The following features are characteristic of this element:
- It is not equipped with a heater, since infrared and convection heat extraction to the steam room is needed.
- It is necessary to provide for the possibility of quick and easy replacement, since this section burns out relatively quickly due to the high heat load.
The second section, starting from the ceiling and facing the street, lasts much longer, so it can be fixed more thoroughly. It must be equipped with a heat insulating sheath. It is installed for several reasons:
- wooden elements of the ceiling and roof, in contact with the chimney, must be protected from overheating (can cause fire);
- preventing the cooling of flue gases, we provide good traction;
- for the same reason, the amount of condensate formed becomes minimal or even zero.
An adapter is installed between both of these parts. In factory-made sandwich chimney kits, this part is called the “starting sandwich”. If it is not installed, the insulation from the second part of the chimney will gradually spill out.
As a heater it is allowed to use only non-combustible materials that are resistant to high temperatures. Polyfoams do not belong to those.
It is best to use basalt wool in the form of a soft mat with a density of 30-50 kg / m3. This heat insulator loses its working qualities when moisture enters and in a bathhouse characterized by high humidity, this drawback must be taken into account. Cotton wool is wrapped in a protective casing made of galvanized steel. The casing is fixed with steel band clamps, and its edges brought together are fastened with self-tapping screws.
In places of passage through the overlap and the roof, a fire cutting is arranged: an additional heat-insulating layer is laid between the chimney and the wooden elements.
Operation of a brick sauna stove
The temperature in the steam room will reach the desired value in about 3-4 hours after the start of kindling. If the furnace manages to cool down strongly between the bath procedures (downtime is more than 3 days), its start must be started with accelerating heating (fuel is laid at 1/3 of the maximum load), which will dry and warm the masonry. If this is not done, microcracks may appear in the walls of the structure, which are especially dangerous in the bathhouse - as was said, in conditions of heat and high humidity, the negative effect of carbon monoxide is much more pronounced.
If it is idle for more than a month, the accelerating furnace should be repeated three times, gradually increasing the volume of fuel portions from ¼ to the maximum.
Such a stove can be operated both in a Russian bath and in a sauna. In the case of a sauna, the intensity of the furnace is slightly increased, and the heater is not watered.
What to drown
Sauna stove can only be wood burning. It is the wood that allows you to warm the steam room in the right way, that is, first the walls, then the air. Coal burns in a slightly different way: first, the light fractions included in its composition quickly burn out, then the phase of prolonged burning of carbon with reduced heat transfer sets in. This mode of combustion is ideal for a heating furnace, but in a steam room it will cause the formation of heavy steam.
Stones for heaters
As mentioned above, stones with high heat capacity and at the same time low heat conductivity are suitable for the heater.
The use of rocks of a metamorphic type - shale, marble, dolomite or limestone - is contraindicated: they are characterized not only by the incorrect ratio of heat capacity to thermal conductivity, but also by the presence of organic impurities, which, when heated, are released in the form of harmful gases. The rocks of volcanic origin with high density are best suited for heaters: talchochlorite, gabbro, diabase and, of course, basalt. The following symptoms are characteristic of them:
- heavy weight;
- dark color;
- fracture is smooth or fine-grained.
It is important to choose the right form of stones. To reduce the proportion of convection heating to 1/3, their surface area per unit volume should be minimal. This requirement is satisfied by the shape of the ball with the smoothest possible surface. Accordingly, stones should be sought as round as possible. The largest can have a diameter of 100 to 150 mm (approximately with a fist or slightly larger), the smallest - from 20 mm.
The way the stones are laid depends on the type of heater. If it is flowing, as in the furnaces described above, then the size of the fraction in the layers should decrease in the direction from the bottom up, that is, the largest stones below, the smallest ones above. When laying a deaf heater, the opposite principle is applied: it is important to ensure the fastest possible transfer of heat from the heated stove to the stones, so the smallest of them (they lie in a denser layer) are laid down.
Video: proper placement of stones in a sauna stove
Sauna stove is significantly different from conventional heating and cooking. And although it is used less often, the construction process should be approached with much greater attention.