How to make a long-burning furnace yourself
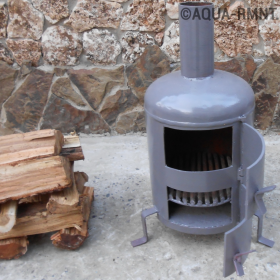
The owners of private houses often have the question of effective and long-term heating of premises with low fuel costs. To combine all these criteria in one furnace, you will need to purchase expensive heating equipment. What to do if such a source of heat is needed, but not enough finance? There is a way out of this situation: you can independently make a long-burning furnace. All that is needed is improvised material, skills in working with a welding machine or work experience as a bricklayer.
Content
What is a long burning furnace, where is it used, its advantages and disadvantages
Long burning furnace It is a heating facility equipped with an additional chamber for combustion of gas emitted by fuel. In such a furnace, the combustion process of the furnace material is slowed down, as a result of which the room is heated for a period from several hours to one and a half days.
Under the influence of a constant temperature, the fuel in the furnace decomposes into wood coke and pyrolysis gas. When interacting with oxygen, the gas begins to burn more intensively, while a large amount of thermal energy is released, sufficient not only for heating, but also for heating water.
Long-burning furnaces differ from traditional designs in that they are supposed to supply oxygen not from the bottom, but from above.
Long-burning furnaces are used to heat cottages, private households, garages, workshops, basements, chicken coops, barns and other household and residential buildings. Depending on the size and modernization of the structure, these heating facilities are also used in industrial premises.
In vernacular, these heating facilities are also called long-burning furnaces.
These efficient heat sources have gained great popularity due to their functional qualities. However, such furnaces have a number of both positive and negative criteria.
Read also how to make a stove for a garage:https://aquatech.tomathouse.com/en/otoplenie/burzhuyka-s-vodyanyim-konturom-svoimi-rukami.html.
Table: advantages and disadvantages of long-burning furnaces
Advantages | disadvantages |
|
|
Types of long-burning furnaces and their choice for self-manufacturing
These stoves are usually made of bricks, metal or stone. They can have a round, cylindrical, square or irregular shape. Depending on their design and method of burning fuel, long-burning furnaces differ in type.
Classic long burning stove
The design, in which the flame propagates from the bottom up, pushing the burning gases through the layers of the flue material, is a classic. This type of furnace is equipped with a heat exchanger and a afterburner, into which an additional portion of air is supplied. Bright representatives of this type are long-burning furnaces: buleryan (branderan), Butakov’s furnace, as well as modified designs with different heat exchangers.
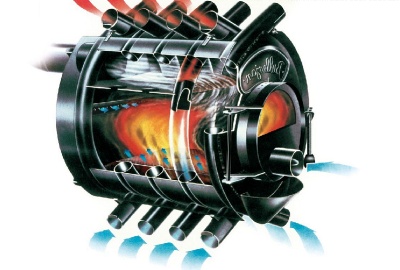
In Buleryan furnaces, the role of a heat exchanger is played by bent pipes located inside the furnace body
Long burning shaft furnace
Another type of such structures is a shaft furnace. In this design, the combustion zone is shifted to the grate part. The products of fuel combustion are discharged through an adjacent compartment in which they burn out, creating heat transfer. This type is best erected from brick, which has been confirmed for many centuries.
Hearth furnace
This is a top-burning structure in which the upper part of the combustion material is ignited, and the direction of fire is in the opposite direction. Such a device requires the supply of oxygen under the burnt layer, so the furnace must contain special air delivery channels. The simplicity of the design, combined with efficiency and functionality, contributed to the creation of many options that you can make yourself. In this case, the used cylindrical containers will serve as the material for its manufacture. A vivid example of this type of heating unit is a stove called "bubafonya".
Gas generating furnaces
Gas generating furnaces or structures with additional pyrolysis gas combustion. In this design, the combustion material burns out under the influence of two factors: high temperature and a small amount of oxygen. This leads to the release of combustible gases, which burn out in the additional chamber. Designs of this type of furnaces are the most difficult to manufacture, however, their efficiency and ease of use are superior to previous versions.
A borelyan stove is considered a hybrid of a potbelly stove and a long burning wood stove. In our next material you will find a description of the principle of operation of this unit, as well as step-by-step installation instructions:https://aquatech.tomathouse.com/en/otoplenie/documents/pech-buleryan-svoimi-rukami.html.
The design of the furnace, its features and principle of operation
Before proceeding with the independent manufacture of the furnace, it is necessary to carefully study all the characteristics of the device.
If it is supposed to make a unit for heating a large room, then the furnace should have a high heat output. For example, for a house or a room of 150 m², you should choose a stove designed for heating up to 200 m². This “reserve” of power is necessary for complete confidence that every corner of the house will be warm.
It is necessary to take into account the fact that not every room adjoins a heat source, so it will take more time and power of the heating device to heat it.
If it is planned to heat a room with an area of 30-50 m², then the furnace can be made without the specified “margin”. In such a small room, heat loss will be minimal, so a unit with a small capacity is enough. Automatic fueling will greatly simplify its maintenance. In the manufacture of such an oven, cooktops for cooking can be provided on its body. If the stove is not only a source of heat, but also an interior item, then windows can be made of refractory glass in its body.
Design features of long burning furnaces
Long-burning heaters have design features that distinguish them from other furnaces:
- the combustion chamber has a volume for loading a large amount of combustible material;
- the case of long-burning furnaces is equipped with a large door;
- the furnace compartment in the furnace body is divided into two chambers; one chamber is designed for smoldering of combustible material, the second - for gas combustion;
- the design of such a furnace provides for the presence of a special chipper that prevents flame from entering the chimney;
- this element of the furnace frame is made of a metal plate, which is welded in the upper part of the furnace compartment.
Differences between conventional and pyrolysis furnaces
To understand the principle of operation of a long-burning furnace, you need to compare it with the operation of a conventional furnace.
The operation of a conventional furnace is to heat its surface and transfer heat to the room. The ignition of the combustion material is carried out from below, which makes the flame spread on the sides, going up. This is due to the access of a large amount of air into the combustion chamber. The fuel in such a furnace burns out quickly, which is why the temperature of the air in the room is unstable - it either drops or rises.
The principle of operation of a long-burning furnace is different. Firewood is burned from above, and the fire spreads downward, while air is supplied only to the burning place. As a result, the material smolders, evenly emitting heat over time. In addition to the combustion material, pyrolysis gas is released, which also serves as fuel, additionally creating heat.
For the manufacture of furnaces, you can use almost any improvised means.In our next article, you will learn how to make a long-burning stove from a barrel:https://aquatech.tomathouse.com/en/otoplenie/burzhujka-dlitelnogo-goreniya-prostaya-konstrukciya-dlya-izgotovleniya-svoimi-rukami.html.
Necessary materials and tools
For the manufacture of a long burning furnace, the following materials will be required:
- a metal barrel from under fuels and lubricants with a capacity of 200 liters; as an alternative material, you can use a steel pipe of the diameter corresponding to the drawing or an empty gas cylinder with a capacity of 50 to 100 l; You can also use sheet steel with a thickness of 3 mm;
- for the manufacture of an air supply channel, a pipe with a diameter of at least 50 mm will be required;
- a chimney requires a piece of pipe with a diameter of 100 mm;
- steel channel or corner piece with a shelf width of 55–65 mm;
- for the air distributor, a metal sheet of at least 3-5 mm, with a diameter slightly larger than the circumference of the housing, is required
- for the manufacture of the lid you will need a steel sheet with a thickness of at least 3-5 mm;
- metal hinges for the door;
- if the furnace body will be equipped with a water circuit, then sheet steel and two threaded pipes will be required.
Tools that can not be avoided in the manufacture of such a furnace are:
- welding machine, electrodes;
- Bulgarian;
- file;
- electric drill;
- metal drills of various diameters (including castellated);
- a hammer;
- anvil or other stable solid surface;
- yardstick;
- building level;
- pencil.
Calculation of the main parameters
A solid-fuel long-burning furnace can be made from improvised materials such as a used gas cylinder, a section of a large steel pipe, or a metal barrel. Material with a wall thickness of at least 5 mm should be selected. This is due to the fact that the smaller thickness of the casing will burn out after some time.
Furnace size
In the absence of any drawings and diagrams for the manufacture of the furnace, you can do all the necessary calculations yourself.
In this case, it would be more accurate to talk about its diameter - D and height - H. These values should be proportional to each other, where a ratio in the range from 1: 3 to 1: 5 is considered optimal. The height of the furnace is usually made at least 100 cm, since this parameter is directly related to the duration of the unit. However, it is not worth making a design too high, since it will be inconvenient to load it with firewood. It can also adversely affect traction. It can decrease so much that the supported flame inside the combustion chamber goes out.
As shown by numerous thermotechnical studies, it is not necessary to make a furnace with a small diameter. From this narrow unit, air is simply drawn into the chimney, which makes the power of the furnace significantly reduced.
If the furnace frame is made too wide, then there will be no uniform burning of fuel near the inner walls of the chamber and in the middle of the hearth. In this case, only the central part of the combustion material will burn out. The metal circle of the piston will sag and clog the hearth, causing the flame to go out. The optimal diameter of this design is from 300 to 900 mm.
Thickness of material used
This criterion must be taken into account, since the thin walls of the case will burn out after some time. In this regard, it is necessary to select material with a thickness of at least 5 mm. This is especially important if you plan to equip the frame with a water jacket, turning it into a boiler. In the image, the wall thickness is indicated by the symbol Δ.
If you use material with a wall thickness of up to 4-5 mm, then this is fraught with the fact that the furnace will lose its power. Due to the thin walls of the body, the temperature will drop over the piston pancake. As a result, the afterburning of pyrolysis gases will decrease, and consequently, the generated heat will decrease.
However, for heating small rooms, such as a garage, a barn or a small workshop, the thickness of such material is quite acceptable.
Metal pancake options
For the effective operation of the furnace, not only the diameter of the round plate on the piston is important, but also its thickness. After all, a metal pancake is a partition and at the same time a heating surface for igniting pyrolysis gases.
When making a metal pancake, you should adhere to the optimal size. The distance from its outer edge to the inner wall of the furnace should be 5%. In the image, this gap is indicated as C = 5% D.
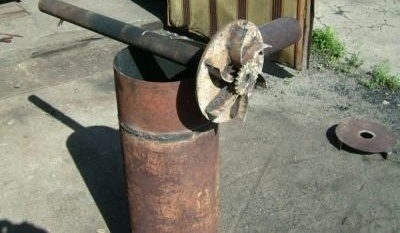
The diameter of the metal pancake should be slightly less than the inner diameter of the furnace body
Outlet Parameters
In the image, the diameter of the chimney pipe is indicated by the letter S. It is recommended that its diameter be at least 80 mm.
Dimensions of the air supply pipe
On the diagram, its diameter is indicated by the letter d. For the design of such a furnace, a pipe of 75 or 80 mm can be used. The pipe must be welded to a metal circle (in its hole in the middle). The result is a part called a piston.
Another option for a long burning furnace is Bubofonya. Description of the principle of operation, calculation of materials, as well as step-by-step installation instructions in our article:https://aquatech.tomathouse.com/en/otoplenie/bubafonya-svoimi-rukami.html.
Preparatory work and selection of the installation site of the furnace
If the furnace will be made of sheet steel, it is necessary to cut it into blanks in accordance with the drawing:
- cut identical fragments from the corners, which will serve as a grate;
- for the manufacture of supports and handles for the case, you can also use metal corners;
- it is also necessary to cut the pipes in advance.
The place for installing the long-burning furnace is selected so that when assembled, it should not be installed closer than 100 cm to the wall.
Since the furnace body will be completely heated, it is necessary to worry about the insulating material in advance. To do this, from a brick, you can build a stand, which should be 30 cm larger than the base of the case. Alternatively, steel bars or corners can be welded to the furnace frame.
At the installation site, from the door to the combustion chamber, it is necessary to lay insulation material. As such, a basalt or asbestos layer is used, on top of which a steel sheet with an area of 100 cm is placed.
Do-it-yourself long-burning stove: diagram and step-by-step instructions
The most common materials for the manufacture of long burning furnaces are metal and brick.
Making a bubafony furnace from a gas cylinder
For independent manufacture of the “bubafony” furnace, a used 50 liter gas cylinder is best suited. The order of the work is as follows:
- Cut off the upper part of the cylinder at the rounding point of the body using a grinder. This fragment will serve as a cover in the future design.
- Weld a metal strip to the upper edge (in the place of the cut of the future cover). Such a side will not allow the lid to move out.
- Next, you need to make a clamping piston, thanks to which the flue material will be pressed during combustion. From a thick steel sheet, cut a circle with a diameter slightly smaller than the body. The circle should freely descend into the cylinder. The gap between the wall of the housing and the circle should be 8-10 mm wide.
- Drill a hole with a diameter of 100 mm in the middle of the circle. It is convenient to do this using a core drill.
- Take a pipe with a similar diameter and weld one end to the middle of the circle. The result is a part with a common hole.
- Then weld four segments of the channel in a cruciform order to the back of the circle.They form a kind of channels through which air will flow into the combustion chamber.
- Weld handles and stands.
- Strip sharp and protruding welding fragments with a file or grinder.
Video: how to make a bubafony stove out of a gas bottle
Making a long-burning brick oven
Of course, in comparison with a home-made metal construction, a brick oven looks more advantageous. However, its independent manufacture is a labor-intensive process that requires certain skills and time.
Foundation preparation
Since the brickwork is quite massive, a solid foundation is necessary for the furnace. The depth of the foundation should ensure the stability of the structure. Foundation preparation is as follows:
- First you need to dig a small pit 30 cm deep. Its width and length should be 10 cm larger than the expected dimensions of the furnace.
- Flatten the bottom of the pit and cover it with roofing material or other insulating material.
- Pour a layer of sand 10 cm thick on top, which must be tamped.
- Pour a layer of fine gravel of similar thickness on top of the sand cushion.
- For reliability of the base it can be reinforced with a metal grill. To do this, use reinforcing bars interconnected by a wire. The width of the grid cells should be no more than 10 cm. The thickness of the rods is selected in the range from 8 to 12 mm.
- Lay the grate in the pit so that it does not touch the bottom. To do this, place fragments of bricks under the metal frame.
- Pour the concrete mix of the M-200 or M-250 brand. Concrete should completely cover the metal frame.
Masonry order
After a few days, when the base hardens, you can proceed to the brickwork of the long-burning furnace. Before starting construction work, it is necessary to soak a brick for a day in water. This must be done so that the brick laid in rows does not draw moisture from the mixture. Bricks should be laid as follows:
- The first and second row must be laid out in continuous layers.
- An ash pan will be installed on the second row, so you need to provide a place for the door.
- On the fifth row above the door, an overlap is installed. Subsequently, a drying chamber box will be installed in it.
- The sixth and seventh row are designed to accommodate the grate and install the door into the combustion chamber.
- From the eighth to tenth row a firebox will be placed. During the laying of the combustion chamber, it is necessary to use a fire-resistant material - fireclay brick. As a bonding agent for masonry, use clay-based mixtures. Ready mixes intended for masonry furnaces are on sale.
- The eleventh row serves as the ceiling of the combustion chamber and forms the area for the chimney. On top of this row, it is necessary to lay steel reinforcement and pour it with a cement mixture.
- On the twelfth row, a place for a hob is formed.
- Starting from the thirteenth to fourteenth rows, rows are laid for the chimney. Its height is made according to individual projects, so the number of rows can be increased several times.
Video: a long burning brick furnace modeled on a children's designer
How to upgrade a long-burning furnace yourself
To make a homemade stove less trouble, it can be improved.
Modernization of the Bubafon furnace
The weight of the “bubafony” furnace construction usually reaches 150–170 kg. This creates inconvenience, since it must be turned over to remove ash and other combustion residues.To avoid this, you can improve the design by making holes in it with doors. However, it should be noted that the peculiarity of such a furnace is precisely in the absence of extra slots through which air can penetrate. Therefore, in the manufacture of doors will require careful sealing in the closed position. This can be achieved by welding metal beads and seals to the body.
The air draft in the combustion chamber will improve if you change the number and shape of the ribs on the round piston plate of the structure. To do this, instead of sections of the channel, you need to weld steel plates. However, they should have a slight bend along the entire length of the part. This form will make it possible to swirl the incoming air, which is evenly distributed in the combustion chamber. From 6 to 8 plates are enough to get the desired effect.
Brick oven upgrade
A long-burning brick oven will take much less space if its design resembles a triangle shape and is placed in a corner of the room. An order of this design will require less building material and, accordingly, financial investments.
The brick version of the long-burning furnace can be upgraded with a separate flap to switch the winter and summer heating mode. In the autumn-spring period, when there are no frosts, but the air is saturated with dampness, this damper will help to make the heating not too hot.
Features of the operation of a long-burning furnace
The functionality and effectiveness of these heating devices depends on the correct operation:
- to reduce the rate of combustion of the fuel, it is necessary to reduce the amount of air supplied to the combustion chamber;
- to avoid condensation in the pipe, it is necessary to calculate the exact number of revolutions and eliminate unnecessary bends;
- it is desirable that the moisture content of the loaded solid fuel does not exceed 20–25%;
- during operation of the furnace, the door of the combustion chamber should not be opened, as carbon monoxide will enter the room;
- 3-4 times a month it is necessary to heat the furnace in maximum mode; this will help burn all the slag accumulated on the walls of the furnace;
- during cleaning furnace it is recommended to use firewood from alder; this wood does not emit intense heat and sedimentary burning;
- the efficiency of the stove will increase if large logs of firewood are laid in it.
Learning how to make a long-burning stove with your own hands, you can get not only a source of heat, but also save money. Having gained valuable experience in the construction of long-burning furnaces, you can help not only friends and acquaintances, but also make it a source of income.