All about pellets: production rules, standards and methods of quality control
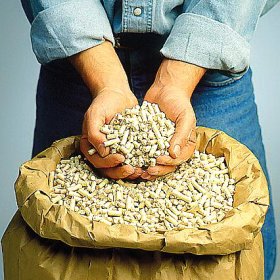
To ensure the operation of pellet heating boilers installed in autonomously operating boiler rooms, pellets are needed. This word borrowed from the English language is called cylindrical fuel granules obtained from wood flour by pressing. The raw materials used for the manufacture of pellets use cracked and non-cracked wood, waste from sawmills, woodworking and furniture industries. Producers of an alternative type of solid fuel also mastered the production of agropellets from straw, corn, sunflower husks, buckwheat husks, etc. When transporting and storing pellets, it is necessary to comply with a number of requirements, which are much softer than the rules for diesel and gaseous fuels. Therefore, the popularity of pellet heating boilers is growing among owners of suburban housing. When buying granular fuel, consumers are interested in its quality, since the efficiency of boiler equipment and the percentage of efficiency depend on this. The quality of pellets is influenced by raw materials, organization of the production process, storage conditions for finished products and delivery to the final consumer.
Fuel granules are formed at a pressure of 300 atm and under the influence of high temperature. At the same time, a special substance called lignin is released from the ground mass, which ensures the bonding of individual fragments into granules.
The length of an individual pellet can vary between 10-30 mm. The diameter of the thinnest granule is 6 mm, and the largest - 10 mm. Pellets are classified as environmentally friendly fuels, since in their production only natural materials are used. When burning granular fuel in pellet boilers, the amount of carbon dioxide emitted into the atmosphere is negligible. Natural decomposition of wood is accompanied by the release of approximately the same amount of carbon dioxide.
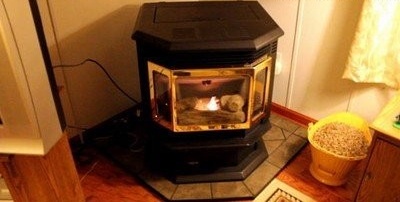
Pellets are an environmentally friendly and very economical fuel used for heating residential premises with fireplaces, stoves, solid fuel boilers
Content
Varietal varieties of pellets
According to the existing classification, fuel granules are divided into three groups:
- white pellets, which are commonly called premium fuel, suitable for high-tech heating boilers;
- dark or industrial pellets, slightly inferior to the first group in quality, since not only wood but also bark is used (suitable for burning in pellet boilers, but with more frequent removal of ash);
- agricultural pellets, considered to be cheap fuel of standard quality, are burned in large boilers produced by manufacturers specifically for this type of solid fuel.
The calorific value of white and dark pellets is the same: 17.2 MJ / kg, and for agropellets lower, 15 MJ / kg. The ash content of premium pellets is 0.5%, dark - 0.7% and higher, agropellet - 3% or more.
The flowability of dry fuel granules is ensured by their cylindrical shape and physico-geometric characteristics (density, abrasion, bulk density). Due to these qualities, fuel can be automatically supplied through special devices used in boiler houses. Automation of the supply of pellets to the heating boiler allows for its long-term operation without the active participation of a person. This is the secret to the success of pellets in the fuel market of many European countries.
The main stages of the production process
Pellet production can be arbitrarily represented in several stages:
- grinding of raw materials;
- drying crushed components;
- regrinding of dried particles;
- water treatment to moisten wood flour;
- pressing crushed and moistened raw materials into granules;
- cooling pellets and cleaning them from dust;
- packing of fuel granules and packaging.
Let's look at each step in more detail.
Stage # 1 - chopping wood raw materials
With the help of chippers, called crushers, they chop wood raw materials into fractions whose length and width are 25 mm and their thickness is 2 mm. Then the crushed raw materials are dried. The smaller the size of the fractions, the less energy is required to dry them.
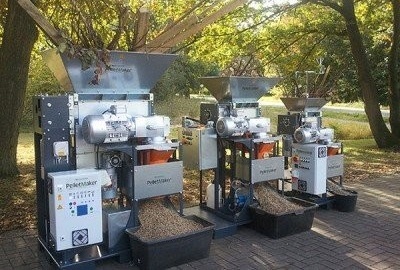
With the help of chippers, called crushers, they provide grinding of wood raw materials into fractions whose length and width is 25 mm
Stage # 2 - drying and regrinding
The moisture level of wood raw materials sent under the press has specific requirements. The percentage of humidity should be 10% with a deviation of 2% in the smaller or larger side. If the raw materials are too wet, additional drying will be required. If the wood fragments are too dry, they will have to be moistened additionally, achieving a 10 percent moisture level.
Drying equipment can be drum and belt type, and the latter option is preferable, albeit more expensive. Using belt dryers is safer. Dryers can be operated on gas or wood waste. There is also a separation of equipment according to the type of drying agent used, which may be water vapor, hot air or flue gases.
Stable operation of the press is possible only if the size of the input fraction of the feed will not exceed 4 mm. Dried raw materials are additionally subjected to grinding in hammer mills, chip machines, disintegrators.
Stage # 3 - Water Treatment
Raw materials whose moisture level does not reach 8% are difficult to compress. To obtain the desired degree of humidity, it is necessary to pass the overdried raw materials through an additional humidification device. The best option is screw mixers, in which steam or water is supplied. Steam has to be used in the processing of wood raw materials obtained from hardwoods. Under the influence of steam, the strength of wood decreases and its plasticity increases.
Presses of a number of manufacturers are arranged in such a way that they do not require preliminary steam exposure to raw materials. Some unscrupulous manufacturers use steam to process old and already caked raw materials. However, it will still not be possible to get good quality pellets from the “revitalized” raw material in this way.
Stage # 4 - pressing
The granulation process is carried out using presses, which are produced by world famous manufacturers: CPM, Salmatec, Andritz, Amandus Kahl, Munch, Buhler, etc. This type of equipment has structural differences, the main one of which is the type of matrix. There are presses:
- with a round matrix (created for use in the food and chemical industries, as well as for the production of animal feed);
- with a flat matrix (created for the disposal of solid waste).
Despite the design differences, the presses of both versions work on the same principle. Running rollers crush the raw materials on the matrix, ensuring its forcing through the provided holes on its surface. The extruded granules are trimmed with special knives. During the pressing process, the equipment manages to compact the raw materials three times.
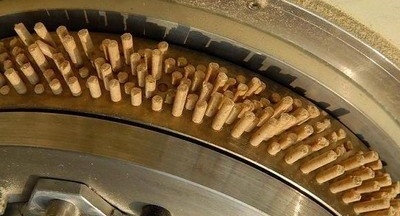
The process of forming pellets using a cylindrical matrix press. Granules of the same diameter are extruded through the holes of the matrix and cut off
The frictional forces in the adiabatic process caused by a sharp compression of the raw materials contribute to raising the temperature in the working area of the press to 100 degrees Celsius. For the processing of tons of raw materials, 30-50 kW of electricity is consumed within an hour.
When granulating wood, the equipment experiences heavy loads, so it is made from especially durable materials. Separate parts of the matrix type are produced from hardened wear-resistant alloys.
Stage # 5 - cooling pellets and cleaning them from dust
The quality of the pellets depends on the degree of effort applied to pressing the raw materials and the temperature at which the formation of the granules takes place. However, there is an upper “ceiling” of temperature values (120 ° C), above which irreversible processes begin to occur in the granulated raw materials, which negatively affect the quality of the pellets.
Compressed granules need cooling, acting on them with a conditioning effect. The equipment of well-known manufacturers is equipped with systems for cleaning finished granules from dust and small crumbs. Pellets are cleaned immediately after the cooling procedure. This has a positive effect on the quality of pellet fuel.
Stage # 6 - pellet packing and packaging
Granular fuel is packaged and packaged in different ways, which allows us to satisfy the diverse needs of consumers. Pellets can be sold in bulk or in bulk bags - the so-called "big bags" containing from 500 to 1200 kg of granules.
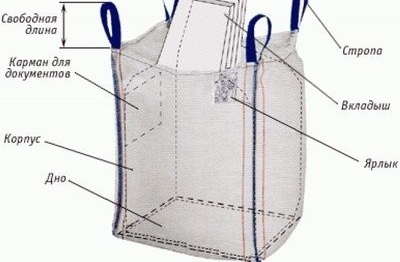
The constituent elements of a huge polymer bag (big bag) used for storing pellets in the warehouses of the manufacturer and subsequent transportation to the bed consumer
In bulk, fuel pellets are dispatched to CHP plants. Although it is possible to ship in bulk and pellets of high quality, which are purchased for heating boilers, as well as for the purpose of further implementation in smaller packaging.
Big-bags are polymer bags equipped with slings for mechanization of loading and unloading operations. Pellets stored and transported in bags do not lose their bulk properties and maintain the required moisture level. However, the purchase of pre-packaged fuel pellets usually costs more than the average consumer.
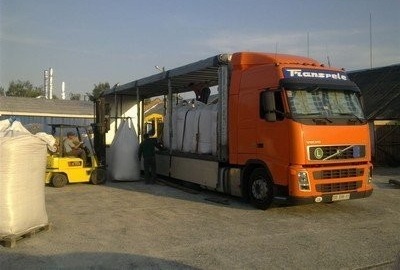
Special trailers for transporting big bags with pellets. Forklift trucks are used to unload heavy bags.
Pellets, packaged in packages of 10-20 kg, are also popular among consumers. Owners of pellet boilers and fireplaces that do not have bunkers for storing large pellet stocks buy them in small packages. Of course, this method of purchasing fuel pellets is considered the most expensive. However, only selected pellets are sold in small containers.
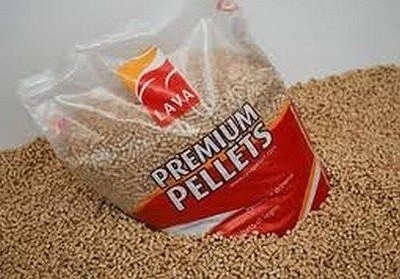
It is more convenient for many buyers to purchase selected pellets packaged in small plastic bags, which are easy to transport in personal transport
What standards determine the quality of pellets?
Russian pellet manufacturers use quality standards adopted in European countries. Foreign manufacturers of fuel for pellet boilers receive certificates of conformity of products to European quality standards. The absence of a document confirming the quality of the pellets scares off buyers. At the same time, the cost of certified products of the same quality is higher than not certified.
The quality standards EN plus and EN-B contain requirements for household and industrial pellets according to a number of criteria, namely:
- diameter
- length
- bulk mass;
- calorific value;
- humidity;
- abrasion (percentage of dust);
- hardness;
- ash content;
- melting point of ash;
- the content of metals and other chemical elements indicated in mg per kg.
Manufacturers who want to win a tender for public procurement of pellet fuel must provide the EN plus certificate in the package of documents.
How not to let yourself be fooled when buying?
When buying pellets, an ordinary citizen should also pay attention to the availability of a quality certificate. In addition to this important document, which dishonest sellers can forge, it is necessary to find out the place of manufacture of the fuel granules. Large manufacturers have regular suppliers of raw materials, under the features of which all technological equipment of companies is configured. From this point of view, large producers will have better pellets.
A visual inspection of the fuel pellets also helps to evaluate the suitability of the product for the operation of pellet boilers. With this control, attention is paid to the color of the granules, the safety of their shape, the amount of dust, the integrity of the surface of the pellets, the absence of pronounced odors, etc. You can order laboratory tests of fuel granules for their compliance with European quality standards. Only for the service provided will have to pay.