Do-it-yourself biofuel: biogas from manure, ethanol for a biofireplace + pellets
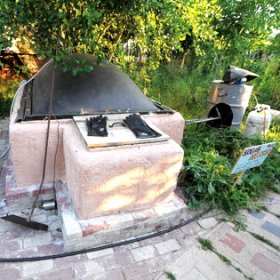
The upcoming fuel crisis has forced mankind to think about searching for fundamentally new sources of energy that could replace traditional gas and oil. There are several fairly promising options. Among them are solar, wind and other types of energy. The use of biofuels is recognized as one of the most effective, which not only gives a good result, but also belongs to the number of budget options. Such fuel is produced from various raw materials. You can even get biofuels from manure with your own hands, this is quite simple.
Biofuel is obtained by biological or thermochemical processing of biomass. For the biological process, various bacteria are used. Different types of animal or vegetable raw materials are used as biomass, as well as animal waste or organic production residues. Quite often used waste wood and plants. There are several types of biofuels:
- Solid. This species includes: peat, fuel pellets and briquettes, wood, wood chips.
- Liquid. These are biobutanol, biodiesel, bioethanol and biobutanol.
- Gaseous. Biohydrogen and biogas.
You can get almost any of the above types of fuel yourself. However, getting some is associated with certain problems. For example, the raw material for liquid biofuels is vegetable oil, which is difficult and expensive to obtain in large quantities. In addition, in the production of biodiesel, it is necessary to work with toxic substances, for example, methanol. Even a small defect in the technological process leads to a loss in the quality of biofuel produced. The simplest option for self-production is biogas.
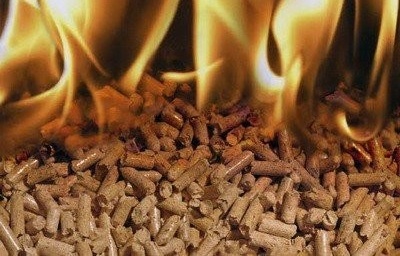
Solid biofuels include fuel pellets. The best quality granules are obtained from waste from woodworking and logging production
Content
How to get biogas at home?
Biogas is called a mixture of gases, which is obtained as a result of overheating of organics. At the same time, air access to raw materials should be stopped. The source material for the production of gaseous biofuels can be grass, various wastes, tops of cultivated plants or manure. The basis of biogas is carbon dioxide and methane. The specific part of the latter can reach 70%. Other gases, for example, hydrogen sulfide, are mixed with this mixture in various proportions.
On average, one kilogram of organics produces about 500 g of gas. Several factors affect the efficiency of biogas production. The most important of them are:
- Ambient temperature. The higher it is, the more intensive is the process of decomposition of organics and the release of biogas.It is no coincidence that the first biogas plants operated in warm regions. However, with sufficient insulation of the installations and the use of hot water in their operation, systems can also be equipped in areas with a cold climate.
- The quality of the raw materials. It should decompose fairly easily. At the same time, its composition should include a sufficient amount of water, without the inclusion of antibiotics, detergents and other substances similar to them, which can slow down the fermentation process.
The simplest device for biogas production at home looks like this. A large pit is being excavated at the site. Concrete rings are laid inside it. So that you get a sealed container. A metal dome is mounted on top of it. Pipes are removed from the tank to the surface for biogas removal. The pit is filled with organic matter. Proven recipe for organic material: mix 3-4 tons of plant waste and 1.5-2 tons of manure. All this is filled with water until a mixture of 60-70% moisture is obtained.
The following material will help to build a bioreactor for biogas:https://aquatech.tomathouse.com/en/otoplenie/alt_otoplenie/kak-poluchit-biogaz.html
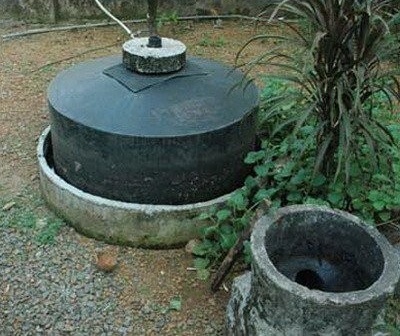
Biogas is a mixture of gases obtained as a result of overheating of organics without oxygen. It is quite easy to get at home. The picture shows a fairly productive biogas plant
Here are some more mix options for biogas production:
- Cow and horse manure mixed in 1: 1 proportions.
- Horse manure mixed with straw or peat.
- Any manure with the addition of flax fire in the ratio of 7: 3.
- Cow dung mixed with sawdust in a ratio of 7: 3.
- Horse manure with the addition of any foliage in a ratio of 7: 3.
- Any manure with the addition of household waste in a ratio of 4: 6.
Prepared raw materials are placed in a container. Using a coil, it is heated to a temperature of about 35 ° C. In such conditions, without the access of air, the fermentation process starts, due to which the mixture is further heated and biogas is released. Gas is piped from the reservoir and enters the accumulator. Such biofuels can be used for heating, cooking and other household needs.
Briquettes from industrial waste are becoming more and more popular every year. Read more about their manufacturing technology here:https://aquatech.tomathouse.com/en/otoplenie/alt_otoplenie/brikety-dlya-otopleniya.html
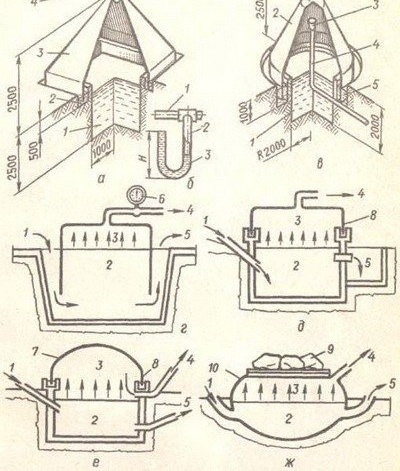
Plants for the production of biogas are quite simple. The figure shows the diagrams of two very simple, but nonetheless effective systems
We make fuel for biofireplaces
All kinds of oils of organic origin become the basis for liquid biofuel. Various alcohol-containing substances are added to them, and also alkali to obtain biodiesel. This is a rather complicated process. At home, the easiest way to make liquid biofuels designed for the fireplace. The so-called biostations do not look completely different from traditional appliances. However, they do not burn wood, but biofuel, which guarantees the absence of carbon monoxide, soot, soot and ash.
Biofireplaces delight their owners with ecological cleanliness and convenience, because there is no need to chop wood and clean ash from such a device. When burned, biofuels decompose into carbon dioxide and water, which are absolutely safe for humans. In this case, the flame is devoid of a characteristic yellow-orange color and looks colorless. This significantly spoils the appearance of the fireplace, giving it an unnatural appearance. Therefore, special additives coloring the flame are necessarily added to biofuels.
For the manufacture of such fuel, 96% ethanol will be needed. It can be purchased at the pharmacy. As a flame coloring additive, you can take gasoline with a high degree of purification. Suitable as a high-quality household brand B-70, and branded for refueling lighters.Outwardly, such gasoline should be completely transparent, there should be no sharp specific smell. 50-100 g of gasoline is taken per liter of alcohol. The resulting mixture is very well mixed.
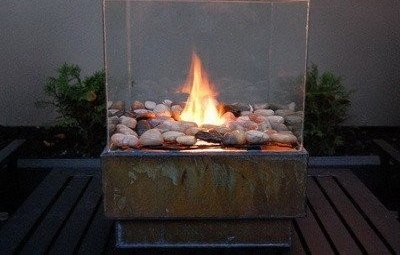
Ecofireplaces are an excellent replacement for traditional appliances. They use environmentally friendly and safe biofuels, which can be made independently.
It should be borne in mind that the composition will stratify over time, therefore it is undesirable to store it. It is best to mix the ingredients immediately before refueling the fireplace. The resulting composition can be used in rooms without exhaust hoods and chimneys, but ventilation, however, is mandatory. On average, about 400-500 ml of home-made biofuel will be required per hour of ecofire work. In addition, the same composition can be used in traditional "kerosene". As a result, we get a perfectly luminous lamp without soot, unpleasant odors and soot.
In order not to freeze near the stove in winter, you need to learn how to heat it. Instructions for proper furnace furnaces can be found in the following article:https://aquatech.tomathouse.com/en/otoplenie/topim-pech-pravilno.html
How to make fuel pellets yourself?
Many owners of autonomous heating systems have already managed to appreciate pellets. This is the name of the granules obtained from the processing of natural fuels, agricultural wastes or wood production. If desired, such biofuels can be made independently.
Industrial production of granules involves several technological stages. They need to be slightly adapted for home production:
- Coarse crushing. During the process, the raw materials are crushed into small particles that are easily dried. A large crusher is used.
- Drying material. The moisture content of raw materials should not exceed 15%. If the humidity is higher, it will not compress well.
- Re-crushing. The material is crushed to particles no larger than 1.5-2 mm in size. A crusher is used for the procedure. Wood chips, fiber shavings and sawdust are crushed with a hammer mill.
- Stirring. At this stage, the moisture level of the raw material is measured. Ideally, it should be 12%. If the moisture content of the product is less than 8%, it should be steamed. For soft coniferous raw materials, you can simply add water to the mixer.
- Pressing. It consists in passing the prepared raw materials through a press with a cylindrical or flat matrix. On sale you can find such equipment designed for working at home.
- Drying and cooling products. Finished pellets are cooled, after which they can be packed in canvas or paper bags and stored.
Here's what it looks like:
Step # 1 - choose the raw materials
For the manufacture of fuel pellets can be used:
- straw;
- chicken droppings;
- peat;
- woodworking waste;
- sunflower husk;
- poor quality wood;
- cereal waste.
The listed components can be used both in pure form and in the form of various mixtures. However, the best raw materials for pellets are agricultural waste, as well as waste from woodworking and logging industries: sawdust, wood chips and bark. Moreover, the most high-quality granules are obtained from coniferous species.
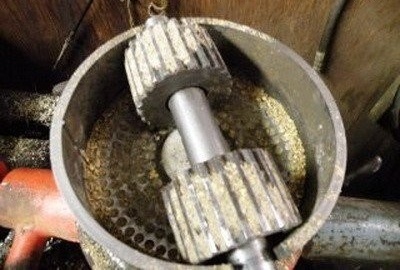
A granulator is used to produce fuel pellets. In the photo - the simplest model with a disk matrix and special gears. You can make such equipment yourself
Step # 2 - select equipment
The main difficulty in producing pellets is the need to purchase or manufacture special equipment. For work you will need:
- Crusher. Such a device can be purchased or manufactured independently. Alternatively, a conventional circular saw can be used for crushing. It will need to install a cutting shaft equipped with flap cutters.Sawdust and small chips can not be crushed.
- Sieve. Designed to separate large particles from sawdust. To make it, you will need to assemble a wooden frame and beat it with a fine metal mesh.
- Dryer. A simple home-made option is a pipe welded from barrels with a remote bottom. The resulting housing is fixed to the bed and rotates quickly using an electric motor. In this case, hot air is supplied into the structure, which dries the sawdust.
- Granulator. Most often, a ready-made installation is purchased, since the device is quite difficult to manufacture.
If desired, the granulator can be assembled independently. The easiest way to make a system with a flat matrix. Actually, the master will have to purchase the main components and independently assemble the equipment from them. The following modules are purchased for the granulator:
- electric motor;
- actuating mechanism;
- gearbox;
- transmission.
The remaining nodes can be done independently. They usually start with a frame. The equipment must be fixed on a rigid, solid base. It can be a construction welded from profile hire: a corner, an I-beam or a channel. The installation can be mobile, then in the corners of the frame it will be necessary to weld the eyes designed to fasten the wheels. The working unit of the granulator can also be made independently. Actually, the actuator is made in the form of a two-section cylindrical tank.
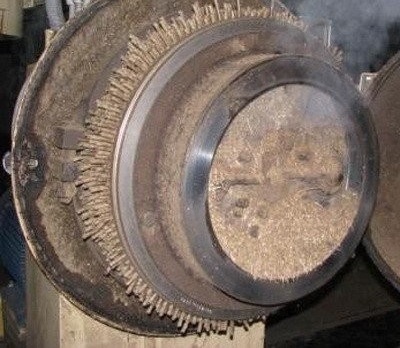
The principle of operation of the granulator for the production of pellets is very simple: the prepared raw material is poured into the equipment, after which it is forced through a hole in the matrix under high pressure. At the output, granules of a given size are obtained
In the first, a matrix-disk and two special gears are fixed on a common shaft. Using a chain transmission, the capacitance is connected to the electric motor through the gearbox. For the manufacture of the matrix you will need a metal sheet whose thickness is 8-10 cm. Cone-shaped holes are made in it, the smaller diameter of which must correspond to the diameter of the finished pellets. The key is attached to the matrix on the vertical shaft of the gearbox. To create a working pressure in the cylinder, a worm pair is installed.
As experience and practice shows, biofuels can be made by yourself. This is a cost-effective solution, despite the certain costs that will have to be incurred when setting up production. This solution is especially effective in the presence of a large amount of raw materials. Renewable sources, low cost, a good substitute for traditional energy - this is not a complete list of the advantages of biofuels. Zealous owners have long been using it in their households. Their experience must be used.
4 comments