Overview of solid fuel boilers: general educational program + which manufacturers should I prefer?
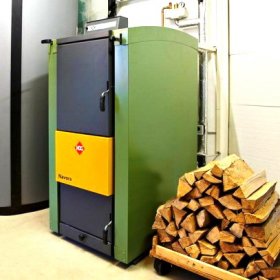
It is extremely difficult to imagine a comfortable house deprived of a heating system, because the presence of heat in a room depends on its availability and functionality. Such a system necessarily includes a heating boiler, the main task of which is to heat the coolant to a predetermined temperature. There are many types of equipment, the main difference of which is the type of fuel used, which determines the principle of operation of the device. According to statistics, the most common heating boilers for solid fuels, considered one of the first heating appliances.
Content
How does such an aggregate work?
Solid fuel devices use various types of solid fuel for their work. This is firewood, coal, oil shale, peat, etc. The cycle of the boiler can be divided into three phases. Let's consider each of them in more detail.
Stage # 1 - ignition of the boiler
The cycle begins with ignition, which is characterized by a sharp increase in temperature on average from 40 ° C to 600 ° C in 5-10 minutes. The temperature values of the furnace heat exchanger begin to grow, which depend on the parameters of the system and can range from 40 ° C to 70 ° C. At a minimum, a heat stroke is possible on the heating system as a whole and on the heat exchanger itself. The latter, especially made of cast iron, will not be able to withstand such conditions for a long time and bursts. If the circulation rate of the coolant is low, and heating takes place quickly, liquid can boil, which will lead to thermal and hydraulic shock to the heating system. The most vulnerable to it are plastic pipes. At this stage, the pipes begin to warm up, but the air in the room is still cold.
Stage # 2 - heating the coolant
The temperature in the furnace continues to rise and reaches 1300 ° C for coal-fired boilers and about 1000 ° C for wood-fired boilers. The coolant continues to warm up. At this stage, control is important, otherwise it may warm up to the maximum temperature of the boiler, which leaves 95 ° C, and this is already dangerous.
Regulation is carried out using a valve that controls the air supply. The optimum temperature should be maintained until complete combustion of the fuel. At this phase, the pipes in the room become hot, the air warms up.
Stage # 3 - Burning Fuel
At the end of the boiler cycle, the fuel completely burns out and smoldering coals form. The temperature drops to 600 ° C-400 ° C, which are considered the most comfortable for the system.The coolant slowly cools, the air in the room also begins to cool down a little. After smoldering coals are formed, the process of cooling the air and coolant is immediately accelerated.
Having examined all phases of the solid fuel boiler operation, you can clearly see its main feature - temperature cyclicity. It is due to the need from time to time to lay a new portion of fuel in order to minimize fluctuations in the temperature of the coolant. To a greater extent, this problem was solved in automatic boilers, where there is an automated fuel supply and pressurization of the burner fan. The rest need constant monitoring by the person and timely replenishment of the fuel supply.
Solid fuel boilers are slightly inferior in terms of efficiency to units operating on liquid fuel. Read more about this heating equipment in our material:https://aquatech.tomathouse.com/en/otoplenie/kotly/kotly-otopleniya-na-zhidkom-toplive.html.
What is a solid fuel boiler?
It should be understood that a solid fuel boiler is a modular design assembled in a steel case, which includes the following components:
- Combustion chamberequipped with a door. This is where the fuel combustion process takes place.
- Grate. Fuel is laid on it and evenly distributed. After burning it, the resulting ash is poured through special holes into the ash pan.
- Cleaning hatch. Designed for cleaning the boiler.
- Heat exchanger. It is a design that transfers energy from a heated coolant to a cold one. Most often this is a barrel through which smoke tubes are laid. The gases passing through them heat the coolant circulating in the heat exchanger.
- Temperature controller for the boiler, allowing you to adjust the rate of combustion of the fuel.
In addition to the above mandatory elements of the device, they can also be equipped with equipment that greatly simplifies their operation. For example, such as a draft regulator, gas burners, a thermostatic valve. Read more about each of them - read on.
Traction control indispensable for adjusting the temperature inside the supply pipe and controlling the access of air to the combustion chamber. The device expands when heated and can affect the damper, opening or, conversely, covering it when the equipment is cooling. Boilers equipped with such a regulator can operate in automatic mode. The device is mounted on the front of the equipment. When the boiler starts up, it is controlled so that the temperature does not fall below 65 ° C and does not rise above 90 ° C.
Traction controllers are also used in pellet boilers. Read more about this in our material:https://aquatech.tomathouse.com/en/otoplenie/kotelnaya/obvyazka-pelletnogo-kotla-otopleniya.html.
Gas-burner It works on natural or liquefied gas and provides many advantages:
- Ignition takes only a few seconds.
- Safety to use.
- Simple design for reliable equipment.
- Possibility of combination with different types of boilers.
- Operation in enclosed spaces.
Thermostatic valve Designed for emergency heat removal from the boiler during overheating. To cool the device, the hot coolant from the system is lowered, and not cold water is pumped in its place. The cooling circuit for steel equipment is installed inside the device, and for cast iron - on the flow.
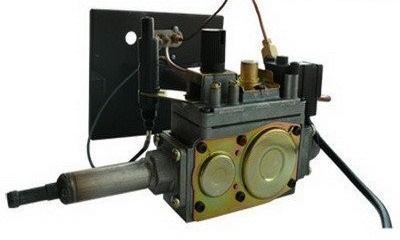
Using a gas burner allows you to get almost instant ignition and safety in the use of the device. This burner can be installed in boilers of any type.
Types of devices based on the principle of fuel combustion
There are several varieties of solid fuel boilers. Let's consider them in more detail.
Option # 1 - classic combustion boilers
The equipment has a large firebox in which fuel combustion occurs naturally. In the design, as a rule, there is a sensor-controller of the coolant temperature, with the function of mechanical adjustment of the air damper. Such boilers are extremely simple in design, which makes their cost relatively small and operation very easy. In addition, they are very unpretentious to the type and quality of fuel and can be heated with coal, as well as wood, briquettes, etc. However, classic devices have disadvantages:
- Short burning time. As practice shows, one bookmark of fuel can last a maximum of eight hours.
- The complexity of automation of heating modes.
- Efficiency lower than other types of solid fuel boilers, which leads to high fuel consumption.
- Non-optimal combustion process leads to increased ash content.
Of all these shortcomings, the problem of frequent fuel loading lends itself to leveling. It is partially solved by installing a heat storage tank, which accumulates heat and thereby smooths out temperature differences of the coolant. The tank is a metal container with good thermal insulation. Its volume is calculated depending on the capacity of the heating system and the capacity of the equipment. However, its presence is an additional cost and the risk of system failure.
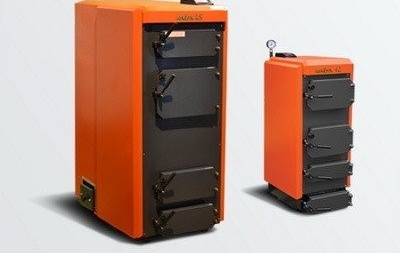
Traditional boilers of classical combustion are very undemanding to fuel. However, due to the design features of their efficiency is lower than that of other devices, therefore, they are characterized by high ash content and high fuel consumption
Option # 2 - long burning apparatus
These boilers lack the disadvantages described above. There are two types of such devices - pyrolysis and smoldering devices. Solid fuel pyrolysis boiler long burning differs from the classic in the presence of two combustion chambers. Fuel begins to burn in conditions of oxygen deficiency. Under the influence of high temperatures, it begins to produce wood gas, the so-called mixture of carbon monoxide, propane, methane and hydrogen. This process is called pyrolysis. At the end of this process, the fuel enters the second chamber, where it is burned with an excess of oxygen. As a result, the efficiency of the system increases to 90%.
Fuel burns up almost without residue, ash has to be cleaned every few days. One load lasts an average of 12 hours. Average fuel consumption is low. Also, the advantages of pyrolysis devices include:
- The ability to maintain a given coolant temperature.
- Work on various types of solid fuels: coal, briquettes, firewood.
- Ample opportunities for automation of combustion control systems.
The disadvantages of the system include a higher cost of equipment, volatility and exactingness to the level of humidity of the fuel.
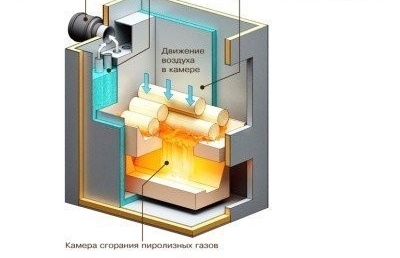
Pyrolysis boilers are distinguished by the presence of two combustion chambers. In the first case, pyrolysis occurs, that is, the release of wood gas, and in the second, the actual combustion of the material
Smoldering devices are distinguished by the presence of a water jacket integrated around the entire perimeter. The combustion process is like a candle - from top to bottom. The process of slow decay of the upper part of the fuel and a large volume of the combustion chamber, and in some cases it reaches 100 l, allows you to stretch the combustion process for a long time.
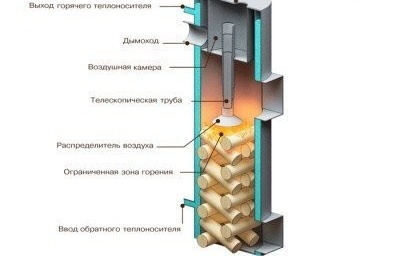
The design of smoldering boilers is such that the fuel ignited from above can burn without adding a new portion for a long time, sometimes up to several days
There are models that can "hold out" on one coal bookmark for five days. To this undoubted advantage of the apparatus, you can add a slightly lower cost than pyrolysis boilers. However, these devices are very demanding on fuel. It should be either coal of the highest quality or wood with a moisture content of not more than 20%.It is necessary to pay attention to the tar content in the fuel, if it is high, frequent cleaning of the system is inevitable, and automation quickly fails.
From our next article you will learn what types of braces are, what are their pros and cons:https://aquatech.tomathouse.com/en/otoplenie/alt_otoplenie/brikety-dlya-otopleniya.html.
Which brands to prefer?
The most famous manufacturers of solid fuel boilers of the classical type of combustion can be considered:
- SAS. The company has more than 30 years of experience in the production of heating equipment. It produces more than nine models of boilers for various purposes.
- Aton. The manufacturer produces three series of devices TTK V, TTK and TRADYCJA. The first two modifications are completely non-volatile, the latter is equipped with automatic control and supercharging.
- Galmet. A large number of variations of various power, designed to work on coal, wood, briquettes, as well as combined models.
- SIME The company offers two types of devices. The range of the Solida brand includes six boilers with power variations from 16 to 40 kW. The Solida Evolution lineup is represented by five devices with a power range of 23-67 kW.
.
The most famous manufacturers of pyrolysis boilers include:
- ATMOS. Models are produced for working on coal, wood or coal, pellets, combined, with the possibility of installing a gas burner.
- VERNER. The company produces VERNER V brand equipment, classic pyrolysis devices designed to operate on biomass. In terms of power, there are two modifications VERNER V45 and VERNER V25.
The most popular manufacturers of devices "smoldering" type:
- Stopuva. Models are produced with a capacity of 10 to 40 kW, working on wood or coal and wood.
- Candle Various power variations are produced, using firewood, wood chips, peat, and briquettes as fuel.
Solid fuel boilers are reliable and practical devices. They make it possible to use almost any type of fuel, which is very convenient. The main disadvantage of classical combustion devices is the temperature differences of the coolant. However, in modifications of long-term combustion, it is absent. This equipment can be fully automated, which makes it possible to use the device with maximum convenience.