Cross-linked polyethylene for underfloor heating: an overview of the best material for “heat-polo-construction”
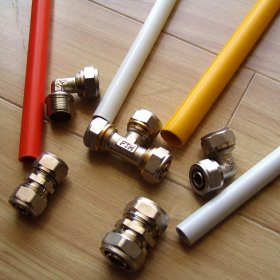
The combination of the words "stitched" and "pipe" until recently caused not the most pleasant associations among developers. Their imagination did not seem to have a particularly strong construction with a longitudinal seam, the main advantage of which was the relatively low price. However, the term “crosslinked polyethylene” with traditional seams has nothing in common. This is a high-tech and quite durable material that is successfully used in construction. Installers are increasingly choosing to use cross-linked polyethylene for underfloor heating.
Content
What is sewn in polyethylene?
In this material, not parts, not sheets, not pipes, but molecules are sewn together. When creating an ethylene polymer, the links of its molecules, due to transverse bonds, form a three-dimensional network with wide cells. Crosslinked polyethylene is produced chemically or physically. Identify the material with the letters PE-X. Depending on the method of production emit:
- PE-Xa - material formed by heating using peroxides;
- PE-Xb - polyethylene obtained after treatment with moisture with an implanted silane and a catalytic substance;
- PE-Xc - product obtained after electron bombardment of polymer molecules;
- PE-Xd - the result of the use of nitrogen technology, is very rare.
Thus, the strength characteristics of crosslinked polyethylene are laid at the molecular level, and it is very difficult to break such bonds. But this is not his only advantage.
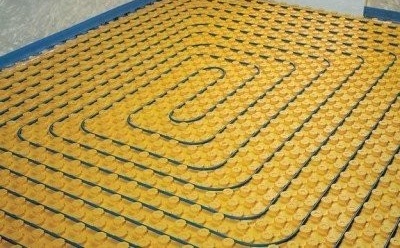
Cross-linked polyethylene is considered the best option for a water heated floor. It is a strong and durable material that absorbs sound perfectly, has good thermal conductivity and is easy to install.
For the installation of underfloor heating systems, experts recommend using pipes obtained using the peroxide method. They are marked with the PE-Xa mark.
What pipes are better to make a warm floor from?
The pipe for the underfloor heating must comply with well-defined requirements, such as:
- resistance to mechanical stress;
- long term of operation;
- resistance to corrosion;
- environmental Safety;
- low coefficient of linear expansion;
- elasticity;
- high heat dissipation;
- ability to absorb noise.
To one degree or another, a number of materials correspond to these characteristics. It is quite successful for the installation of water floor heating systems using pipes from:
- copper;
- corrugated steel;
- metal plastic;
- polypropylene;
- polyethylene.
Copper pipes are an upscale and time-tested option. However, their cost is high in itself. In addition, you will need to spend money on the polymer shell required when installing copper in the screed, and on special brass fittings.
It is easier to work with corrugated steel and its consumption will be slightly less, with almost the same operational characteristics as copper. But the price of the material will be just as high.
Metal-plastic constructions are relatively “young” and perfectly fulfill the role of a transport line during the installation of a warm floor. However, over time, scale may build up inside threaded fittings. In addition, during installation, the probability of a pipe cut is high.
In polypropylene pipes, with such advantages as an affordable price, easy installation and low physical weight, the linear expansion indicators are “lame” when heated. When mounted in a concrete screed, they must be reinforced with fiberglass and aluminum.
Pipes made of cross-linked polyethylene are considered the most modern choice for installing a warm floor, since their characteristics correspond to technological requirements to the fullest extent. Among the shortcomings can be noted the lack of flexibility of the material, because of which the pipes do not hold well during installation.
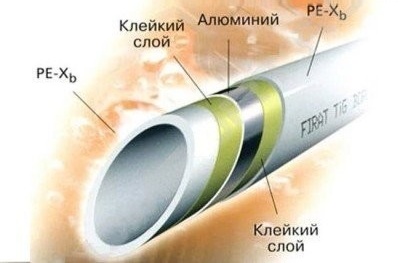
The pipe made of cross-linked polyethylene with anti-diffusion protection includes a special layer of aluminum, which prevents the penetration of oxygen or water vapor through the walls of the pipe
Note! Cross-linked polyethylene is successfully used not only for the installation of underfloor heating, but also in water supply systems. Problems can arise due to the high oxygen permeability of this material, which can lead to increased corrosion processes on individual structural elements. Therefore, for underfloor heating, it is recommended to use only pipes with special anti-diffusion protection.
STOUT brand offers a wide selection of pipes, fittings, manifolds and other types of products for utility networks
Cross-linked polyethylene vs metal-plastic pipe
Although the assortment of pipes for underfloor heating is very diverse, as shown above, in practice the master usually offers the client a choice between two options: metal-plastic structures and pipes made of cross-linked polyethylene. It should be noted immediately that at the price there is no big difference between polyethylene and metal plastic. In both cases, you can save a little if you find material at a bargain price.
Therefore, experts recommend focusing on the characteristics of the operational characteristics of the material. When mounting complex diameters, cross-linked polyethylene behaves somewhat worse. Than a plastic pipe. In rooms with a small area or when implementing a complex scheme for laying a warm floor, it is still recommended to pay attention to metal-plastic constructions. But in all other cases, a cross-linked polyethylene underfloor heating is a more practical option.
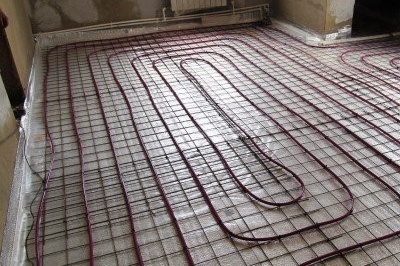
When installing a cross-linked polyethylene underfloor heating, some caution should be observed, since the pipe does not keep its shape very well in places of bends
Some installers are of the opinion that cross-linked polyethylene is more reliable than multilayer metal-plastic constructions. It is also noted that Pex perfectly tolerates freezing and does not burst, even at the joints with fittings. The burning temperature of cross-linked polyethylene is 400 degrees. Under such conditions, the material melts and turns into liquid droplets. In the process of combustion, it decomposes into completely safe substances: water and carbon dioxide.
Crosslinked polyethylene is not afraid of ordinary solvents. Neither aliphatic solvents (gasoline and its “relatives”), nor aromatic (such as toluene), nor chlorinated hydrocarbons (eg trichlorethylene) will cause any noticeable harm to the pipes. Care should be taken when working with hard-to-volatile organic compounds such as fats, oils, waxes, etc.Contact with them may cause some swelling of the crosslinked polyethylene. Ordinary antifreezes, detergents and anticorrosive agents do not cause cracks in pipes made of cross-linked polyethylene. But such strong oxidizing agents as nitric acid and halogens can completely destroy the material. Do not allow pipes to come into contact with these hazardous substances.
Features of installation of pex pipes
The process of laying a warm floor is presented in detail in the following video:
When installing pipes made of cross-linked polyethylene, compression and pressure fittings can be used. The easiest way to work with the first option. To install a compression fitting, you must:
- Slip a crimp nut onto the pipe with the thread directed toward the connector.
- Push the split ring onto the pipe so that its edge is 1 mm from the pipe cut.
- Push the pipe onto the fitting plug until it stops.
- Tighten the compression nut with wrenches.
When installing compression fittings, you do not need to try to remove the chamfer from the pipe. In addition, tighten the compression nut very carefully, as excessive force can damage the pipe.
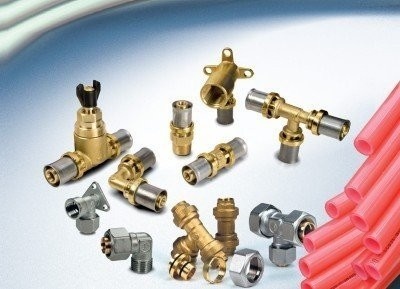
Pipe fittings made of cross-linked polyethylene are very diverse. Their installation does not require special skills or sophisticated equipment
Press fittings allow for one-piece connection of cross-linked polyethylene pipes. To implement this option, you will need special press equipment. It is done like this:
- First, a continuous clamping sleeve is put on.
- Then, into the pipe, you need to fully insert the expander of the appropriate size.
- The handles of the expander should be smoothly reduced to the stop and locked in this position for a few seconds.
- Insert the pipe into the fitting socket until it stops.
- Press the sleeve onto the fitting using a manual or hydraulic press.
Crosslinked polyethylene has a molecular memory, therefore, it is subject to reverse shrinkage. Already a couple of minutes after the pipe is inserted into the socket, it will be very difficult to remove it from the fitting.
2 comments