Analysis of the most popular mistakes when welding polypropylene pipes
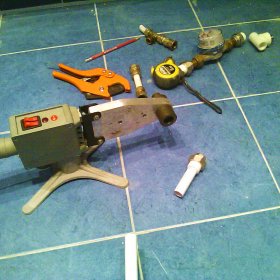
From the side it seems that there is nothing particularly complicated in welding polypropylene pipes: it is ready to heat, connect, cool. However, in practice it turns out that in this case there are many important points that affect the quality of the connection of pipes and fittings. Neglect of these nuances leads to various flaws that cause blockage, pipe leakage and other problems. Some errors are detected only a few months after the start of operation of the pipeline, when the unfortunate craftsmen had already caught a trace.
Content
A little bit about the soldering process
For welding pipes and fittings made of polypropylene, the method of thermal polyfusion is most often used. Its essence is to heat the parts to be welded to a certain temperature and quickly connect them. To warm up the parts, a special device is used, popularly referred to as a “soldering iron”. The process of soldering plastic pipes is graphically presented in the video material:
What types of polypropylene pipes are and how to properly solder and join, read in our next article:https://aquatech.tomathouse.com/en/uchebnik/truby/rabota-s-polipropilenovymi-trubami.html.
Some manufacturers of heaters for soldering plastic pipes install two heating elements on one device at once. (This is typical for low-cost models of Chinese and Turkish production). A separate switch is provided for each of them, and the power of each such element is enough to heat pipes and fittings of a specific diameter. You should not use two heating elements at the same time, so as not to overheat the plastic, not to overload the network and not to consume excess electricity. The second heater should be used as a spare, necessary in case of breakdown of the first.
If the welding tool is equipped with two heating circuits, they can be switched on at the same time at the beginning of work in order to quickly heat up the tool. Then one of the circuits should be turned off.
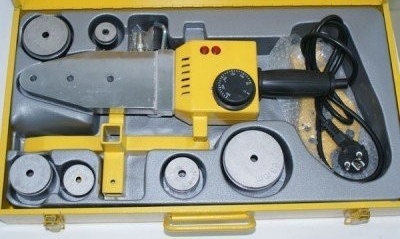
The use of the device for welding pipes made of polypropylene does not require special skills. However, novice installers should practice a bit before starting work.
The heated pipe material retains ductility for some (very short) time. In these seconds, you need to connect the elements and fix the connection, while eliminating distortions. Only at the end of the “fixation” phase, when the material loses elasticity, can the connected pipes be laid on the table.
The optimum temperature for heating polypropylene pipes is considered to be a temperature of 260 degrees. In the process of heating, it is necessary to warm up the pipe material strongly enough to ensure a reliable connection. At the same time, the pipe must not be overheated so that it does not lose shape. To do this, monitor the heating time.Depending on the diameter of the pipes, it can be:
- 8-9 seconds for pipes with a diameter of 20 mm;
- 9-10 seconds for pipes with a diameter of 25 mm;
- 10-12 seconds for pipes with a diameter of 32 mm, etc.
If the pipe is not warmed up to the required temperature, the connection will be too weak, over time a leak will form there. Overheating of the pipe can lead to flooding and reduce its permeability.
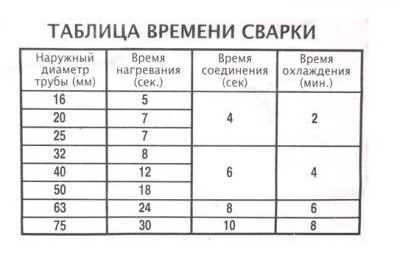
The table shows the estimated time for welding polypropylene pipes, depending on their diameter. Do not violate these deadlines, so as not to spoil the work
There are models of devices for soldering polypropylene pipes with or without temperature adjustment knob. The ability to vary temperature was dictated more by the marketing considerations of the manufacturer than by practical necessity. Professionals recommend setting the temperature correctly (260 degrees) and in the future do not change it, focusing on the heating time. Therefore, the old models of "soldering irons", in which there is no regulator of the heating temperature, are quite suitable for high-quality welding of polypropylene pipes.
The pipes are heated and connected, now it is important to cool them correctly. It takes as much time to complete the “fixation” phase as it does to heat. Inexperienced masters are in a hurry, they stop the process before these few seconds, which causes the connection to deform. Do not think that to work with pipes made of polypropylene, a stopwatch is absolutely necessary. Experienced craftsmen calculate the heating-cooling time automatically, without any instruments.
The range of errors made when welding polypropylene pipes is quite extensive. Most often it is:
- Contamination at the junction of elements
- A small amount of water that has fallen on the material during the welding process
- Long positioning of pipe parts
- Using inappropriate or substandard material
- Non-observance of installation rules, etc.
It is not difficult to avoid these errors if accuracy, care and a high professional level of performers are observed during welding.
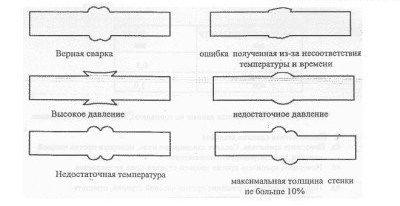
The figure schematically shows the appearance of correct and improper butt welding of polypropylene pipes. To avoid such errors, it is necessary to comply with the installation technology
You may also find useful material about choosing a soldering iron for polypropylene pipes:https://aquatech.tomathouse.com/en/uchebnik/svarka/payalnik-dlya-polipropilenovyx-trub.html.
Error # 1 - dirt and water on the connected elements
A professional installer must wipe all the parts to be welded before starting work to remove possible contaminants. You should also pay attention to the condition of the floor in the room where the welding is performed, since the pipes are laid on the floor and dirt gets on them again. When dismantling a faulty pipe, it is often possible to find a clear strip of dirt along the entire length of the connection.
Remaining water in the pipe can be fatal to the connection. A few drops during heating turn into steam, the material is deformed and loses strength. To remove water from the pipe, it is enough to fill it with salt or to push the crushed bread crumb inside. At the end of work, the pipe, of course, should be thoroughly flushed. The connection with such flaws can remain stable even when crimping, but after some time (sometimes it can take a whole year), a leak will certainly appear. A similar error occurs when welding stabilized pipes, if the foil from the intermediate layer is removed carelessly. Even a small piece of foil at the junction will significantly impair the quality of installation.
Not only pipes, but also a soldering iron should be clean. The master should promptly remove particles of molten polypropylene from all elements of his tool, otherwise they will fall onto the next pipe.
Error # 2 - incorrect positioning
After the two heated parts of the pipe are connected, the master has only a few seconds to put them correctly relative to each other.The shorter this period, the better. If the time limit is exceeded, the deformation becomes irreversible and the bond strength decreases.
Inexperienced craftsmen sometimes try to immediately remove swarms that appeared during the welding process. You should not do this, since a non-cooled connection at this moment can be easily deformed. Flush should be removed after cooling the connection. And it’s even better not to overheat the pipe, then floats simply will not appear.
Error # 3 - incorrect material
If inexpensive low-quality polypropylene pipes are chosen for installation, even the most skillful installation will not protect home owners from damage. Pipes and fittings are best purchased from the same reliable supplier, choose a good company, etc. Avaricious pays twice.
Another problem of this kind is an attempt to connect two high-quality pipes from different manufacturers. The chemical composition of such elements may vary, so such pipes will behave differently when heated. Under such conditions, it is almost impossible to achieve a reliable connection.
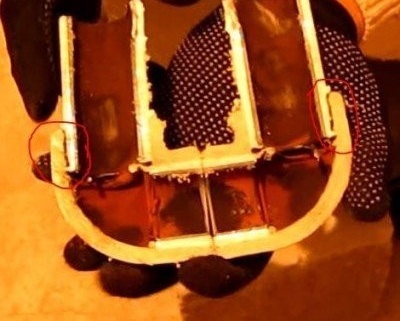
Visual result of improper soldering of polypropylene pipes in the section. The use of low-quality material and non-observance of the time of the “fixation” phase led to deformation of the joint
Error # 4 - neglecting installation rules
The poor quality of welding polypropylene pipes can be caused by various errors during the connection of the fitting and the pipe. For example, if the pipe is not fully inserted into the fitting, a gap is formed between its edge and the fitting's inner stop. As a result, a place appears where the inner diameter is larger and the wall thickness is less than planned. The design operating pressure for such a site will not be high enough, normal loads may be excessive here, which will lead to leakage.
Excessive force is also not permissible when introducing the heated edge of the pipe into the fitting. In this case, significant sagging may form inside. As a result, the pipeline traffic will be lower than the calculated indicators, which will negatively affect the operation of the pipeline.
Read also our next article, which provides instructions for installing a heating system using polypropylene pipes: https://aquatech.tomathouse.com/en/otoplenie/documents/montazh-otopleniya-iz-polipropilenovyx-trub.html
Sometimes the cause of the violation is ordinary human laziness or negligence. For example, a fitting damaged in the process of pipe soldering must certainly be replaced with a new one. If the necessary parts were not at hand, negligent craftsmen simply solder the fitting end-to-end with the pipe. Such a connection will last for some time, but over time, the leakage problem will still have to be solved.
After cutting the workpieces, the internal and external edges of the cut must be carefully cleaned with a scraper. Of course, in the absence of the proper tool, you can use improvised means, for example, a hacksaw for metal, but when it is used, polypropylene will inevitably melt.It will be necessary to chamfer the workpieces, and this will require an additional waste of time and effort.
Finally, I want to recall that the lion's share of defects appears after welding carried out on weight. The only exceptions are cases that arise in particularly difficult, curved sections of the highway, or when completing the installation of a separate branch. The soldering (welding) machine must have a stand stable enough so that the unit does not tip over during operation.
5 comments