The main methods and technology of cementing wells
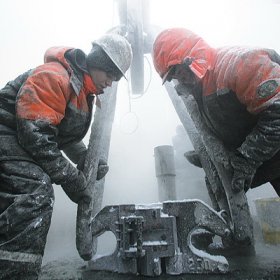
At the final stage of drilling, well cementing is carried out. The viability of the entire structure depends on the quality of this operation. The main goal that is pursued during this process is to completely replace the drilling fluid with cement, which is also called grouting. The injected solution should harden within a certain time interval and turn into a cement stone. Several methods have been developed for cementing wells, with the most common of them being over a hundred years old. The direct one-cycle casing cementing method was developed in 1905 by engineer A.A. Bogushevsky living in Baku. Until now, this technology with minor improvements is used by drillers.
In this video, a diagram of continuous cementing of the annulus through the shoe is graphically presented:
Process components
The cementing process consists of five main types of work:
- preparation of cement slurry;
- injection of the prepared solution into the well;
- supply of cement mortar in the selected manner into the annulus;
- hardening period of the injected grouting mortar;
- quality control of cementing work using available methods.
Important! Before starting work, a program of their implementation is drawn up, which is based on the technical calculation of well cementing. At the same time, mining and geological conditions, the length of the interval that needs to be strengthened, the design features of the wellbore and its condition are taken into account. In the calculation, they rely on the experience of similar work in the area, if any.
Schemes for filing cement slurry in the annulus
Existing methods of cementing wells differ from each other by the method of supplying cement (grouting) mortar into the annulus, as well as by the features of the devices used for this. There are two options for organizing the supply of the prepared solution:
- a direct scheme, which involves pumping a solution into the casing with its subsequent passage to the shoe and subsequent entry into the annulus, filling up from the bottom;
- the reverse scheme is characterized by the supply of grouting mortar from the surface into the annulus, while the injected mixture moves from top to bottom.
When drilling wells on an industrial scale, the cementing method is most often used, carried out in a straightforward manner. In this case, the cementing process can be carried out in one cycle, during which the entire volume of the solution necessary for plugging is pressed immediately.
Schematic representation of a single-stage cementing process:
I. The beginning of the process of supplying cement to the wellbore.
II.Feeding a portion of the solution pumped into the well down the casing.
III. The beginning of the process of forcing the grouting material into the annulus.
IV. Completion of the process of pressing cementing material.

The scheme of single-stage (single-cycle) well cementing: 1 - Pressure gauge for monitoring pressure; 2 - Cementing head; 3 - Top plug; 4 -Cork bottom; 5 - Cemented casing; 6 - Well walls; 7 - Stop ring; 8 - Liquid for punching cement material; 9 - Drilling fluid; 10 - Cement mortar
In very deep wells, resorting to two-stage cementing. The entire front of work is divided into intervals, which are filled with the help of special equipment in turn.
Along with the listed options for cementing casing strings, there is also a cuff method in which part of the trunk is protected from penetration of grouting mortar. Using the cuff, the area located in the interval of the reservoir is isolated.
In a separate group, it is customary to single out methods of cementing secret sections and columns.
Important! All cementing methods pursue one goal, which is to displace drilling fluid from the annular space of the well with the help of cement, which must be raised to a given height, according to the calculations.
The selected cementing technology should provide:
- filling with grouting mortar the entire interval of the trunk along the entire length of its length;
- complete displacement of the wash liquid with cement mortar within the cemented interval;
- protection of grouting mortar from ingress of flushing fluid;
- obtaining a strong cement stone with high resistance to mechanical and chemical influences, capable of withstanding the high loads experienced by the walls of the barrel at a depth;
- good adhesion of the hardened cement stone with the walls of the well and with the surface of the casing.
Important! Ensuring the quality of the casing cementing process allows you to significantly increase the durability of these deep structures and the production period through their operation of the desired product.
Types of equipment you may need
The list of technical support for the work includes the following equipment for cementing wells:
- cementing aggregates necessary for mixing cement and forcing it into a well under pressure;
- cement mixing machines are used for the same purposes as cementing machines;
- a cementing head is necessary for flushing the borehole and subsequent cementing of its walls;
- filling plugs are used if two-stage cementing of wells is selected;
- other types of small equipment, including high-pressure valves, flexible metal hoses, mortar distribution devices, etc.
Important! To ensure the quality of the implementation of a complex engineering task, it is necessary to strictly follow the requirements of the technological regulations developed by specialists for fastening wellbores. Also, the grouting team, which includes only skilled workers, must observe technological discipline. Great attention is paid to the quality of the grouting materials used.
As you can see, the process of cementing wells depends on the professionalism of the people involved in the work, and on the materials used to complete the task.